The Power of Checklists: Ensuring Consistency, Accuracy, and Compliance in Maintenance Engineering

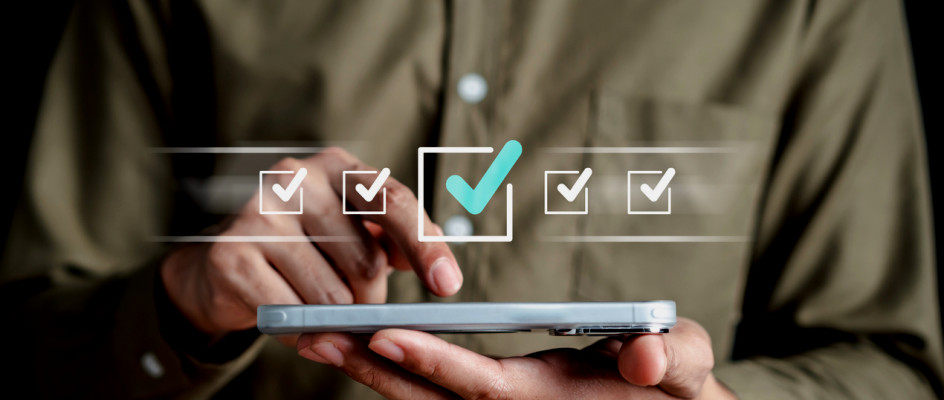
When it comes to maintenance management & maximizing your asset uptime, efficiency, reliability, and compliance are non-negotiable. Tasks must be performed accurately, deadlines met, and safety regulations followed to the letter.
But how can teams consistently deliver high-quality results, especially when dealing with complex systems and processes? The answer lies in a simple yet powerful tool—checklists.
A Brief History of Checklists
Checklists have been a part of human history for centuries, from ancient scrolls cataloguing inventory to maritime logs ensuring voyages were well-stocked and organized. However, their modern application gained prominence in the 1930s when the aviation industry adopted checklists to improve safety and prevent oversights during aircraft inspections. Since then, checklists have been widely adopted across industries including healthcare, construction, and maintenance engineering.
The aviation industry, in particular, demonstrated how a structured approach to tasks could dramatically reduce errors and improve outcomes. Pilots and ground crews began using checklists to ensure no critical steps were overlooked during pre-flight inspections and emergency procedures. This approach has since been applied across industries where precision and safety are essential.
Why Checklists Matter in Maintenance Engineering
Maintenance engineers often operate in environments where even small errors can lead to costly breakdowns, safety hazards, and compliance violations. Checklists provide a systematic approach to managing tasks, ensuring nothing is overlooked.
1. Consistency Across Processes
Checklists act as a standard operating procedure (SOP) that ensures each maintenance task is carried out the same way, every time. This consistency is crucial for:
Preventing variability in results.
Maintaining uniformity in inspections and repairs.
Simplifying training for new engineers.
Establishing repeatable workflows that improve efficiency over time.
Consistency is particularly valuable when multiple team members are involved in the same process. With a checklist in place, it becomes easier to transfer knowledge and maintain performance standards regardless of who is executing the task.
2. Accuracy Through Guidance
With step-by-step instructions, checklists reduce the likelihood of human error. They help engineers stay focused, especially during repetitive or complex tasks. By following a checklist, teams can:
Avoid skipping critical steps.
Track progress easily.
Document completed tasks for future reference.
Identify gaps or inconsistencies that may require process improvements.
For example, in equipment maintenance, failing to tighten a bolt or lubricate a joint can lead to catastrophic failure. A checklist prevents these oversights by serving as a reliable guide.
3. Compliance and Accountability
Regulatory compliance is a major concern in industries where safety standards must be upheld. Checklists provide a documented trail of work completed, demonstrating adherence to regulations. They also:
Serve as audit tools during inspections.
Offer evidence for certifications and approvals.
Enhance accountability by assigning responsibility for each task.
In heavily regulated industries, such as manufacturing and energy production, compliance is non-negotiable. Checklists not only help meet legal and safety requirements but also protect organizations from fines, shutdowns, and reputational damage.
Types of Checklists in Maintenance Engineering
Preventive Maintenance Checklists – Focus on routine inspections, lubrication, and part replacements to avoid unexpected failures.
Safety Inspection Checklists – Ensure that equipment meets safety standards before and after use.
Troubleshooting Checklists – Guide engineers through systematic problem-solving steps to identify and resolve faults.
Shutdown and Startup Checklists – Provide structured procedures for safely shutting down or restarting systems.
Compliance Checklists – Address regulatory and industry-specific requirements.
Emergency Response Checklists – Ensure that proper procedures are followed in case of emergencies, such as equipment failures or safety incidents.
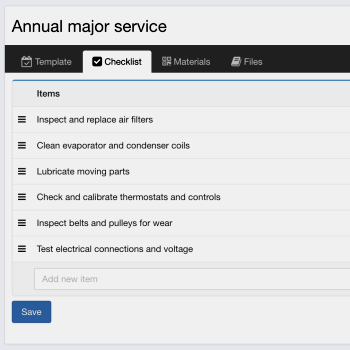
Key Benefits of Checklists for Maintenance Engineers
Improved Productivity – Engineers can work more efficiently by following predefined steps, saving time and reducing rework.
Reduced Downtime – Preventive maintenance checklists help catch issues early, minimizing unexpected equipment failures.
Better Resource Management – Track inventory and spare parts more effectively by integrating checklists into inventory management systems.
Enhanced Communication – Digital checklists allow teams to share updates in real time, improving collaboration and transparency.
The Digital Transformation of Checklists
While paper-based checklists have served their purpose, modern maintenance teams are increasingly turning to Computerized Maintenance Management Systems (CMMS) to digitize workflows. Digital checklists offer:
Real-time updates and collaboration.
Mobile accessibility for field engineers.
Automated reminders and task tracking.
Analytics to monitor performance and identify areas for improvement.
Integration with IoT devices to trigger alerts and maintenance schedules.
Digital tools enhance the usability of checklists by making them more interactive and adaptable. For example, a CMMS can send alerts when a task is overdue or notify supervisors of incomplete steps, ensuring higher accountability.
Best Practices for Implementing Checklists
To maximize the effectiveness of checklists, organizations should:
Customize Checklists for Specific Needs – Avoid generic templates; tailor checklists to the equipment and tasks involved.
Train Employees on Proper Usage – Provide clear instructions on how and when to use checklists.
Regularly Update Checklists – Review and revise checklists to incorporate feedback and evolving standards.
Monitor Compliance – Use analytics to track completion rates and identify areas for improvement.
Integrate with CMMS – Leverage technology to streamline checklist management and reporting.
Case Study: Checklists in Action
Consider a manufacturing plant that implemented digital checklists as part of its preventive maintenance program. By standardizing procedures and tracking compliance, the plant reduced unplanned downtime by 30% and extended the lifespan of critical equipment. Engineers reported fewer errors and increased confidence in their work, demonstrating the power of checklists as a transformative tool.
Conclusion
For maintenance engineers, checklists are more than just task lists—they are essential tools for ensuring consistency, accuracy, and compliance. Whether paper-based or digital, checklists bring structure and reliability to work execution, empowering teams to maintain high standards while mitigating risks. As technology continues to evolve, integrating digital checklists into CMMS platforms will further streamline processes and improve operational efficiency.
By adopting checklists, maintenance engineers can keep their operations running smoothly, minimize downtime, and ensure compliance—all while delivering exceptional results. With a clear framework in place, teams can focus on achieving operational excellence, enhancing safety, and driving long-term performance.
Try Maintainly's CMMS checklists free for 14 days here.