Top 8 Implementation Tips for CMMS Software

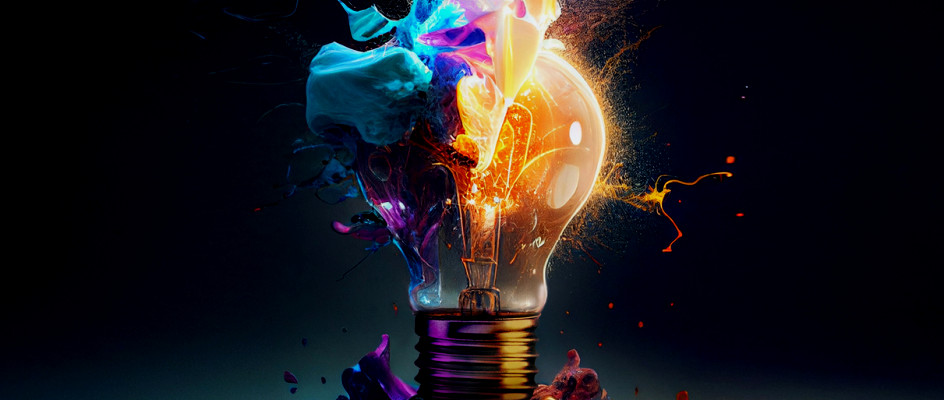
In the fast-paced world of modern business, efficient maintenance management is essential to keep operations running smoothly. At the heart of effective maintenance management lies the powerful tool known as CMMS, or Computerized Maintenance Management System. CMMS, often integrated with Work Order Management Software, empowers organizations to streamline their maintenance operations, reduce downtime, and cut costs. But adopting CMMS isn't a one-size-fits-all solution. To maximize its benefits, you need a well-thought-out implementation strategy.
In this blog, we'll delve into nine crucial tips to ensure a successful CMMS implementation that transforms your maintenance operations.
What's Most Important When Implementing CMMS Software?
The following eight tips will help you implement CMMS successfully, or at least help keep them at the front of mind when going through the CMMS selection process:
Tip #1: Define Clear Objectives
Before diving into CMMS implementation, you must establish clear objectives. Pose the question to yourself: "What are our objectives with this system?" Whether it's reducing downtime, improving asset reliability, enhancing overall efficiency, or achieving specific cost-saving goals, having well-defined objectives will guide your implementation process. Ensure that your CMMS aligns with your organizational needs and priorities.
Additionally, consider the scope of your objectives. Are you implementing CMMS across the entire organization, or is it initially being introduced in specific departments? Having a phased approach can make the process more manageable and allow for fine-tuning as you expand its use.
Tip #2: Involve Key Stakeholders
Gather input from various departments, including maintenance teams, IT, and management. Ensure that all key stakeholders are actively involved in the decision-making process. Their insights and feedback can help tailor the CMMS system to meet specific requirements and increase buy-in from all parties involved.
Furthermore, establish a clear communication plan to keep stakeholders informed throughout the implementation process. Regular updates and open channels of communication will help address concerns and ensure everyone understands the benefits of CMMS.
Tip #3: Plan Data Migration Carefully
Transferring existing maintenance data into the CMMS is a critical step. Pay meticulous attention to data migration, ensuring that all historical maintenance records, equipment details, and work order histories are accurately transferred. This step is vital to maintaining a seamless transition and preserving valuable historical data.
Consider creating a data migration team responsible for validating data accuracy and completeness. Having dedicated personnel focused on this task will help prevent data discrepancies and ensure a smooth transition.
Tip #4: Provide Comprehensive Training
Implementing CMMS effectively requires that your team understands how to use the system. Offer comprehensive training sessions to all users, covering everything from basic functionality to advanced features. A well-trained team will make the most of the CMMS, ensuring a higher ROI in the long run.
Training should extend beyond the initial implementation phase. Plan for ongoing training and refresher courses to keep your team's skills up to date and enable them to fully utilize new features and updates as they are rolled out.
Tip #5: Ensure Ongoing Support
CMMS software implementation is a continuous and evolving process, not a one-time occurrence. Ensure that you have a support system in place, whether it's from the software provider or an internal team. This support will help you address any issues, stay up to date with software updates, and keep your CMMS running smoothly.
Consider creating a dedicated support team or designating individuals within your organization as CMMS champions. These individuals can serve as the go-to experts for troubleshooting, training, and keeping the system aligned with evolving business needs.
Tip #6: Establish Mobile Accessibility
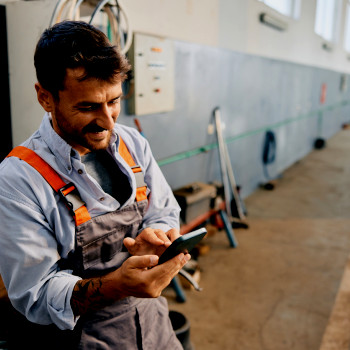
In today's mobile-driven world, ensuring mobile accessibility for your CMMS can significantly enhance its utility. Enable your maintenance teams to access work orders, asset information, and maintenance histories from their mobile devices. This mobility allows for real-time updates, quicker response times, and improved productivity in the field.
Make sure the mobile interface is user-friendly and supports essential functionalities like creating and updating work orders, capturing images, and scanning barcodes for equipment identification.
Tip #7: Embrace Predictive Maintenance
To take full advantage of your CMMS, consider incorporating predictive maintenance capabilities. These technologies utilize data and analytics to predict when equipment is likely to fail, allowing for proactive maintenance. By leveraging IoT sensors and machine learning algorithms, your CMMS can help you reduce unplanned downtime and extend the lifespan of your assets.
Tip #8: Monitor and Adjust
After the initial implementation, continuous monitoring is essential. Regularly review performance metrics and gather feedback from users to identify areas for improvement. Adjust your CMMS configuration and processes accordingly to optimize its efficiency over time.
Establish key performance indicators (KPIs) to track the system's effectiveness. These KPIs can include metrics related to maintenance costs, asset uptime, work order completion times, and more. Regularly analyze these metrics and use them to drive continuous improvement efforts.
In conclusion, implementing Maintainly CMMS software, integrated with Work Order Management Software, can revolutionize your maintenance operations. By following these nine implementation tips—defining clear objectives, involving key stakeholders, careful data migration, comprehensive training, customization, continuous monitoring, ongoing support, establishing mobile accessibility, and embracing predictive maintenance—you can maximize the benefits of CMMS, optimizing your maintenance processes for increased efficiency and cost savings. So, don't delay in harnessing the power of CMMS to transform your maintenance management and drive your organization's success. With the right approach and commitment to these tips, your CMMS implementation can lead to a more streamlined, efficient, and productive maintenance operation.