CMMS for Manufacturing: Prevent Downtime and Maximize Output

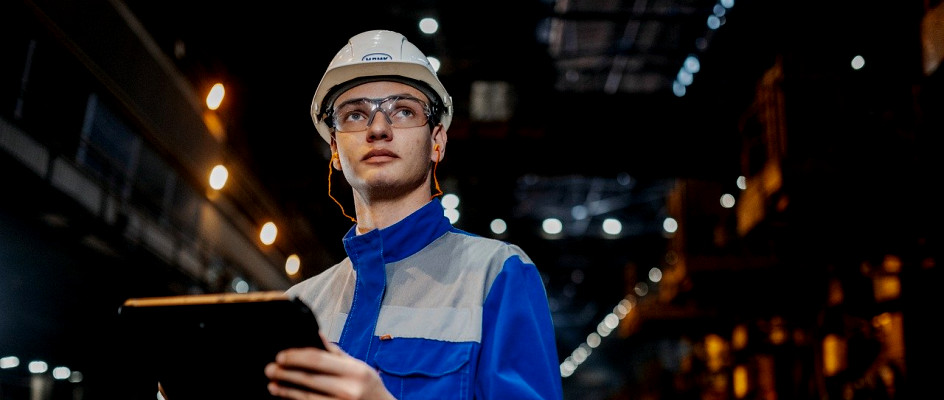
If you run or manage a manufacturing industry, downtime or sudden malfunction is the last thing you would want. A single unscheduled halt in production can ripple across the supply chain, delay deliveries, frustrate customers, and eat into profits.
Luckily, there's a smarter way to deal with this recurring problem: Computerized Maintenance Management Systems (CMMS).
These platforms are revolutionizing maintenance practices across manufacturing sectors. Whether you're a maintenance supervisor at a mid-size plant or running operations for a global manufacturer, CMMS can help you predict, prevent, and eliminate unnecessary equipment downtime.
Let's discuss how it works and why you can't afford to ignore it.
What Is a CMMS?
First, a quick primer. A Computerized Maintenance Management System (CMMS) is software that helps organizations plan, track, and optimize all maintenance activities from scheduling preventive maintenance to tracking spare parts inventory to logging equipment failures. In short, it's the central hub for all things maintenance-related.
The Cost of Downtime in Manufacturing
Before we talk solutions, let's look at the problem.
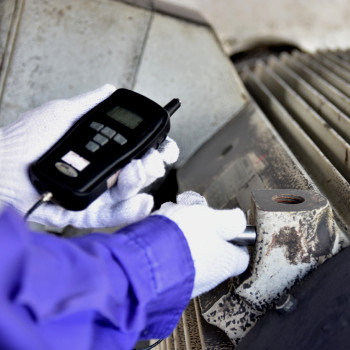
Unplanned downtime is expensive. According to a 2022 study by Siemens, the average cost of downtime in manufacturing is around $260,000 per hour. That number spikes dramatically depending on industry, equipment, and scale. For large manufacturers, downtime can run into the millions.
Here's what's at stake:
Lost Production Output: When a machine is down, the ripple effect can halt entire lines. Suddenly, you're missing shipment windows, frustrating customers, and risking penalties.
Skyrocketing Repair Costs: Emergency fixes are always more expensive. You're paying overtime labor, premium shipping for parts, and burning cash with every passing hour.
Reduced Equipment Lifespan: Without regular upkeep, machinery breaks down faster, forcing early replacements and major capital investments.
Team Disruption: Maintenance crews must drop scheduled tasks to deal with fire drills. Other departments suffer delays too.
Safety Hazards: Sudden malfunctions can cause unsafe working conditions, putting employees at risk and opening the door to compliance issues or legal action.
In high-output industries like automotive or food processing, even one minute of downtime can cost thousands of dollars.
Common causes of downtime include:
Lack of Preventive Maintenance
Equipment failure
Lack of spare parts
Delayed maintenance
Human error
Poor visibility into asset conditions
Many of these issues are preventable. And that's the key. You can simply use a reliable CMMS like Maintainly to react faster when things go wrong.
How a CMMS Prevents Downtime?
Here's how a good CMMS works its magic:
1. Preventive Maintenance Scheduling
With a CMMS, you can schedule maintenance based on time, usage, or condition. For example, you can set up a preventive maintenance task to inspect and lubricate a conveyor belt every 100 operating hours. The CMMS tracks usage, notifies the technician, and ensures the task is completed before a breakdown occurs.
This proactive approach keeps equipment in peak condition and minimizes unexpected failures.
2. Asset History and Maintenance Logs
Every asset has a history, like when it was installed, what's been fixed, how often it breaks, and which parts usually fail. A CMMS maintains a complete digital history for each asset. That means technicians can review previous issues and repairs before working on a machine, helping them diagnose problems faster and avoid repeating mistakes.
3. Work Order Management
Gone are the days of scribbled notes and lost service requests. A CMMS gives you a streamlined, centralized system to create, assign, and track work orders in real time. This transparency ensures accountability and better coordination between departments. Managers can monitor progress, prioritize urgent tasks, and ensure nothing slips through the cracks.
4. Inventory and Spare Parts Management
Ever needed a part for a critical repair, only to find out it's not in stock? A CMMS tracks inventory levels of spare parts and materials, alerts you when stock is low, and can even automate reordering. This ensures that the right parts are always available when needed, reducing downtime caused by waiting for deliveries.
5. Condition Monitoring and Predictive Maintenance
Modern CMMS platforms can integrate with sensors and IoT devices to enable condition-based maintenance. Let's say your press machine starts vibrating beyond normal levels. The sensor detects it, the CMMS flags it, and a technician is alerted before a critical failure occurs. This is what we can call predictive maintenance. It helps you fix what needs fixing before it breaks.
Real-World Benefits: Maximizing Output
Now let's flip the coin. Preventing downtime is huge, but maximizing output is just as important. By implementing predictive analytics and automated work order management, many reputed manufacturing companies like Ford cut downtime by 40%.
A well-implemented CMMS can lead to:
Higher Equipment Availability: When machines are regularly maintained and rarely down, they're producing more. It's as simple as that.
Improved Workforce Efficiency: Technicians spend less time tracking down parts, paperwork, and previous records and more time fixing what matters. With mobile access to CMMS tools, they can close out work orders, update logs, and upload photos from the shop floor.
Better Compliance and Safety: CMMS tools help maintain compliance with industry regulations and safety standards by ensuring inspections are completed on time and issues are documented. This reduces the risk of accidents and fines.
Smarter Decision-Making: With detailed analytics and reporting, you can identify patterns, spot underperforming assets, and make informed decisions about repairs vs. replacements.
Choosing and Implementing the CMMS for Manufacturing
Step 1: Audit Your Current Maintenance Program
Document what equipment you have, how often it fails, and your current response process. Look for bottlenecks and paper trails.
Step 2: Choose the Right CMMS
Not all CMMS platforms are built the same. If you've used legacy systems before, you know the pain with clunky interfaces, rigid workflows, limited access, and complex features.
Modern manufacturing demands a smarter, more connected approach to maintenance. So when evaluating your options, keep an eye out for a CMMS that offers:
IoT integration
Corrective and Predictive maintenance
Mobile access
Asset changeouts
Maintenance team communication
Custom task labels
User-friendly dashboards
Cloud-based accessibility
Maintainly every box. It is built to keep your team focused on maintaining equipment, not maintaining software. Explore its other features here↗
Step 3: Train Your Team
Even the best software is useless if your team doesn't know how to use it. Train for both function and value to help them see why it matters.
Step 4: Track KPIs
Monitor metrics like:
MTBF (Mean Time Between Failures)
MTTR (Mean Time To Repair)
OEE (Overall Equipment Effectiveness)
PMP (Planned Maintenance Percentage)
Measuring Success: What to Watch?
Once implemented, a good CMMS should show measurable gains. Track the following:
Less Downtime: Is MTBF increasing?
Faster Repairs: Are technicians resolving issues faster?
Lower Maintenance Costs: Are you spending less on emergency repairs?
More Planned Maintenance: Are you scheduling more and reacting less?
The Bottom Line: CMMS as a Competitive Advantage
In manufacturing, the pressure to do more with less is constant. Labor shortages, rising material costs, and tighter margins all push you to squeeze every drop of efficiency out of your operation.
A CMMS isn't just a tool for the maintenance team. It's a strategic advantage. It helps prevent costly breakdowns, improve output, and empower your workforce with the tools and insights they need to succeed.
Whether you're managing a small fabrication shop or a multi-site production empire, a well-deployed CMMS can help you shift from firefighting to future-proofing.
So the question isn't "Can you afford to invest in a CMMS?"
It's "Can you afford not to?" Try Maintainly free for 14 days.