Demystifying CMMS Maintenance Terms: Understanding PMs, CM, Reactive, and Corrective Maintenance

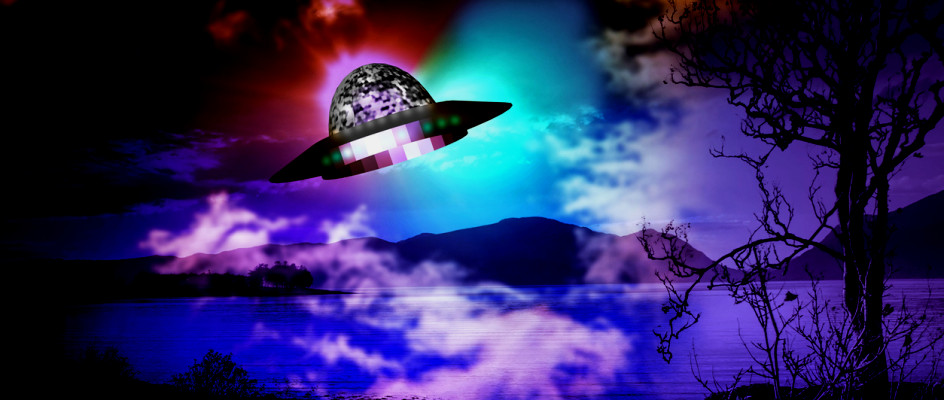
Navigating through the plethora of CMMS terminologies can be akin to deciphering a complex code. From Preventive Maintenance (PM) to Corrective Maintenance (CM), and Reactive Maintenance to Condition-Based Maintenance, each term carries specific nuances that play a pivotal role in the efficient functioning of an organization. We'll unravel the key maintenance terms within the context of a Computerized Maintenance Management System (CMMS), shedding light on their definitions, purposes, and the crucial differences that set them apart.
1. Preventive Maintenance (PM)
Definition:
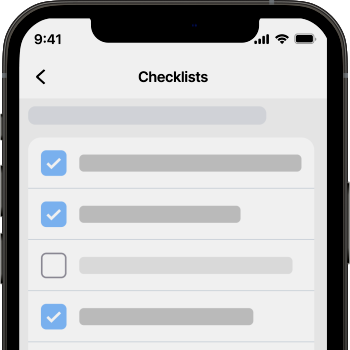
Preventive Maintenance (PM) is a proactive approach to maintenance that involves regular, scheduled tasks aimed at preventing equipment failures and optimizing the performance of assets. These tasks are carried out at predetermined intervals and are designed to address potential issues before they escalate into more significant problems.
Time-Based and Metric-Driven Maintenance:
Traditionally, preventive maintenance has relied on time-based schedules, where tasks are performed at fixed intervals (e.g., weekly, monthly, or annually). However, modern PM programs increasingly incorporate metric-driven triggers to optimize maintenance efforts further. Metrics such as equipment runtime, vibration levels, temperature readings, and pressure levels can provide real-time insights into the condition of assets. When these metrics deviate from normal operating parameters, they can signal the need for maintenance, even if the scheduled time interval has not yet elapsed.
Purpose:
The primary purpose of preventive maintenance is to extend the lifespan of equipment, reduce the risk of unplanned downtime, and enhance overall reliability. By systematically conducting inspections, pre-defined checklists, lubrications, adjustments, and replacements, organizations can identify and address potential issues before they lead to costly breakdowns.
Benefits:
Improved Equipment Longevity: Regular upkeep helps to prevent wear and tear, prolonging the life of assets.
Reduced Downtime: Proactive maintenance minimizes unexpected failures and associated downtime.
Cost Efficiency: Addressing small issues early prevents costly repairs and unplanned stoppages.
Enhanced Safety: Properly maintained equipment reduces the likelihood of accidents and hazards.
Resource Optimization: Metric-based triggers ensure maintenance is performed only when necessary, avoiding over-maintenance or neglect.
By combining both time-based schedules and real-time metric analysis, organizations can create a robust preventive maintenance program that maximizes efficiency and ensures equipment operates at peak performance.
2. Corrective Maintenance (CM)
Definition:
Corrective Maintenance (CM) is a reactive approach to maintenance that involves addressing issues and failures as they occur. Unlike preventive maintenance, corrective maintenance is not scheduled but rather initiated in response to equipment malfunctions, breakdowns, or performance issues.
Purpose:
The purpose of corrective maintenance is to restore equipment to its operational state promptly. It aims to fix problems as they arise and minimize downtime. While corrective maintenance is essential for addressing unexpected failures, it is typically more costly and can lead to disruptions in operations.
Benefits:
Immediate Response: Quickly addresses equipment issues to restore functionality.
Reduced Initial Costs: No upfront scheduling or routine tasks means lower initial expenditure compared to PM.
Flexibility: Allows for adjustments and repairs as issues emerge, without the constraints of a fixed schedule.
Problem Resolution: Tackles specific problems directly, often leading to immediate fixes.
Essential for Unpredictable Failures: Provides a critical response mechanism for unforeseen equipment malfunctions.
3. Reactive Maintenance
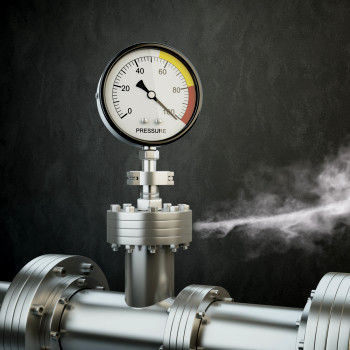
Definition:
Reactive Maintenance, often used interchangeably with Corrective Maintenance, refers to maintenance activities initiated in response to unexpected equipment failures or breakdowns. The focus is on addressing issues after they occur, and the maintenance team reacts to the problem rather than proactively preventing it.
Purpose:
The primary purpose of reactive maintenance is to restore equipment functionality quickly and minimize downtime. While it is a necessary approach for addressing urgent issues, relying solely on reactive maintenance can lead to increased costs, as emergency repairs tend to be more expensive than planned preventive measures.
Benefits:
Quick Problem Resolution: Allows for immediate attention to equipment failures, minimizing operational delays.
Simplified Planning: No need for complex scheduling or advanced planning, as tasks are handled as issues arise.
Lower Initial Investment: Does not require upfront costs associated with regular inspections or planned maintenance programs.
Focus on Critical Failures: Ensures resources are directed toward urgent and high-priority issues.
Minimal Administrative Overhead: Reduces the need for extensive documentation or maintenance planning systems.
4. Condition-Based Maintenance (CBM)
Definition:
Condition-Based Maintenance (CBM) is a data-driven approach that involves monitoring the actual condition of equipment to determine when maintenance should be performed. This method relies on real-time data from sensors and other monitoring devices to assess the health and performance of assets.
Purpose:
The purpose of Condition-Based Maintenance is to optimize maintenance activities by performing tasks only when there is evidence that they are needed. CBM aims to reduce unnecessary maintenance and associated costs while ensuring that maintenance interventions are timely and effective.
Benefits:
Reduced Maintenance Costs
By performing maintenance only when necessary, CBM minimizes unnecessary servicing, reducing labor and material expenses.Improved Equipment Reliability
CBM ensures timely maintenance interventions, preventing unexpected failures and extending equipment lifespan.Increased Operational Efficiency
Real-time monitoring allows for better resource allocation and minimizes downtime, boosting productivity.Enhanced Safety
Identifying potential issues early reduces the risk of accidents caused by equipment failures.Data-Driven Decision Making
The use of real-time data enables informed maintenance scheduling, better planning, and continuous improvement of processes.
5. Predictive Maintenance
Definition:
Predictive Maintenance is an advanced maintenance strategy that uses data analytics, machine learning, and predictive modeling to forecast when equipment failures are likely to occur. This approach involves analyzing historical data, monitoring current conditions, and predicting future issues.
Purpose:
The purpose of Predictive Maintenance is to proactively address potential problems before they result in equipment failures. By predicting when maintenance is needed based on data trends and patterns, organizations can optimize resources, reduce downtime, and extend the life of their assets.
Benefits:
Minimized Downtime
Predictive maintenance reduces unexpected equipment failures, ensuring smoother operations with fewer interruptions.Cost Savings
By addressing issues before they escalate, organizations avoid costly repairs and replacements while optimizing maintenance budgets.Extended Equipment Lifespan
Timely interventions prevent excessive wear and tear, increasing the longevity of assets.Improved Resource Allocation
Predictive insights enable more efficient scheduling of maintenance tasks and better use of labor and materials.Enhanced Operational Efficiency
Advanced data analytics provide actionable insights, allowing businesses to maintain peak performance while minimizing disruptions.
Key Differences in Types of Maintenance
1. Timing of Intervention:
Preventive Maintenance and Predictive Maintenance are proactive approaches, addressing issues before they lead to failures.
Corrective Maintenance and Reactive Maintenance are reactive approaches, responding to issues after they occur.
2. Scheduled vs. Unscheduled:
Preventive Maintenance and Predictive Maintenance are scheduled and planned activities.
Corrective Maintenance and Reactive Maintenance are unscheduled, initiated in response to unexpected events.
3. Focus on Downtime:
Preventive Maintenance and Predictive Maintenance aim to reduce unplanned downtime.
Corrective Maintenance and Reactive Maintenance focus on minimizing downtime after an issue has occurred.
4. Cost Implications:
Preventive Maintenance and Predictive Maintenance may involve upfront costs but aim to reduce overall maintenance expenses by preventing major failures.
Corrective Maintenance and Reactive Maintenance can be more costly due to emergency repairs and unplanned downtime.
5. Data-Driven vs. Event-Driven:
Predictive Maintenance and Condition-Based Maintenance rely on data and real-time monitoring.
Corrective Maintenance and Reactive Maintenance are event-driven, responding to failures or issues as they happen.
Conclusion
Understanding the distinctions between these key terms is essential for organizations seeking to optimize asset performance, minimize downtime, and control maintenance costs. By strategically incorporating preventive, corrective, and predictive maintenance approaches within a robust CMMS framework, organizations can strike a balance that aligns with their operational goals, ensuring the reliability and longevity of their assets. As technology continues to advance, the integration of data-driven strategies, such as Condition-Based Maintenance and Predictive Maintenance, offers new avenues for organizations to elevate their maintenance practices and move towards a more proactive and efficient future.