Preventive Maintenance for Small Companies: How to Make CMMS Accessible

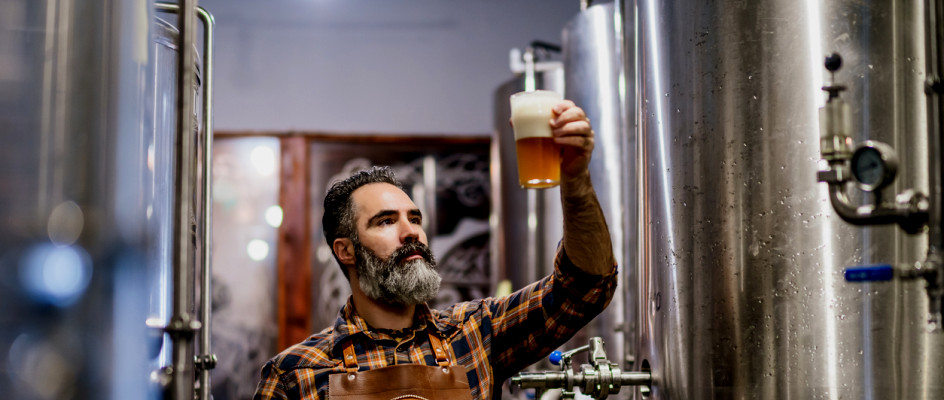
For small companies, every piece of equipment matters. Whether you're running a fabrication shop, a boutique manufacturing business, a small hotel, or a service-based company, unplanned equipment breakdowns can cost you more than just repair bills. They can halt your operations, frustrate your team, and damage your reputation with customers.
That's why preventive maintenance (PM) is so important, and increasingly non-negotiable, even for small businesses.
But here’s the catch: most small business owners already wear multiple hats, and the idea of implementing a computerized maintenance management system (CMMS) can seem intimidating. Isn’t it expensive? Complicated? Time-consuming?
It doesn’t have to be.
In this post, we’ll walk through how small businesses can take a smart, phased approach to preventive maintenance, how to select an accessible CMMS, and how to ensure it actually gets used without draining time or budget.
Why Preventive Maintenance Is Critical for Small Business
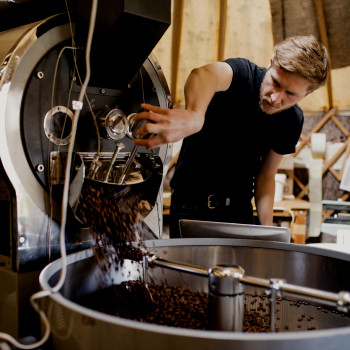
The myth that preventive maintenance is only for big corporations has done real damage. In reality, smaller businesses may have more to lose from unplanned downtime. Here’s why:
Less equipment redundancy: You likely don’t have spare machines sitting idle.
Tighter margins: One missed order or delayed service hits harder.
Smaller teams: A breakdown eats into valuable technician time.
High impact per failure: A failed HVAC unit in a small hotel or a dead compressor in a bakery affects your entire operation.
Preventive maintenance helps avoid these risks by making sure assets are checked, cleaned, adjusted, or serviced at optimal intervals. This results in:
Reduced emergency repairs
Longer equipment life
Improved safety
Lower long-term costs
Even for a team of two, PM is a worthwhile investment—and with modern CMMS tools, it's more practical than ever.
The Shift: Why CMMS Is No Longer Out of Reach
Until recently, implementing a CMMS required big budgets, dedicated IT teams, and a tolerance for clunky software. That’s changed. Over the past few years, several trends have made CMMS tools vastly more accessible to small businesses:
Cloud-based systems remove the need for local servers or installations.
Mobile-first platforms allow technicians to update work orders from the field.
Freemium models and modular pricing mean you only pay for what you use.
Intuitive user interfaces make training almost unnecessary.
Modern CMMS platforms are built to grow with your business, not overwhelm it.
Making Preventive Maintenance Work for Your Small Business
So how can a small company realistically adopt preventive maintenance and a CMMS without overloading its team?
Here’s a practical guide:
1. Start With Just One or Two Critical Assets
Don’t try to build a fully loaded asset database on day one. Instead:
Identify the most failure-prone or essential equipment.
Ask yourself: “What would shut down my business if it broke today?”
Begin logging basic maintenance tasks on those assets.
Example: For a small printing company, this could mean servicing the press’s rollers every 100 hours or checking for belt tension monthly. Start there.
2. Use a Lightweight, Mobile-Friendly CMMS
Choose a CMMS that supports real-world use in the field. A good system for small business should:
Be usable on phones and tablets
Have minimal setup time (hours, not weeks)
Require little or no training
Be simple enough for a non-tech person to use
Look for vendors that offer:
QR code tagging to quickly pull up asset history
Voice-to-text notes for fast logging
Checklists for recurring maintenance steps
Offline mode, so technicians aren’t stuck if they lose signal
Bonus points if the CMMS has automation for scheduling recurring tasks.
3. Phase In Over 21 Days (Not All at Once)
Implementing CMMS doesn't need to be a massive project. Use a phased approach:
Phase 1 – First 7 Days:
Set up your first 1–3 assets
Create 1–2 preventive tasks per asset
Assign work orders to yourself or your team
Track completion manually or through the app
Phase 2 – Next 7 Days:
Add more assets gradually
Begin using the reporting features to track time and cost
Invite more team members to use the system
Phase 3 – Final 7 Days:
Refine workflows: automate task assignments, create custom templates
Start using the mobile app full-time
Export basic reports to see your maintenance trends
By the end of 21 days, your team will have a rhythm and real data to work with.
4. Select a CMMS with the Right Features for You
Don’t be dazzled by dozens of features you’ll never use. Here are the core features that matter most for small companies:
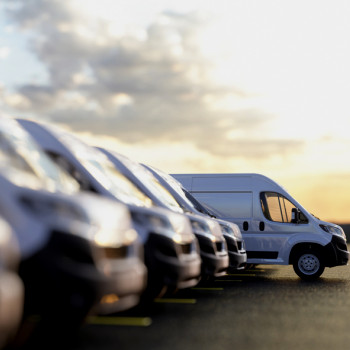
Essential Features:
Work Order Management: Easily create, assign, and close tasks.
Asset Database: Track location, age, service history, and part numbers.
Recurring Maintenance Scheduling: Automate PM tasks on time or usage intervals.
Mobile Access: So your team can use it anywhere, anytime.
Basic Reporting: So you can see what’s working—and what’s not.
Features to Skip (for now):
Deep integrations with ERPs
Multi-site inventory forecasting
Custom API scripting
Enterprise procurement workflows
Focus on ease-of-use over power—you can always upgrade later.
5. Look for Low-Cost or No-Cost Options to Start
Many platforms offer:
Free trials (14 to 30 days)
Freemium plans with core features for small teams
Pay-as-you-grow pricing, so you only pay when you scale
Some CMMS solutions even offer per-user pricing or monthly subscriptions with no annual lock-ins. This lets you experiment without long-term risk.
Ask potential vendors:
Do you charge setup fees?
Is there a minimum user requirement?
What’s included in your lowest tier?
Can we upgrade as we grow?
6. Get Buy-In Without Burning Out Your Team
For preventive maintenance and CMMS adoption to stick, you need your team on board. Here's how:
Keep expectations realistic: Don’t dump a full system on them overnight.
Explain the “why”: Show how PM prevents headaches and saves money.
Celebrate early wins: Highlight when PM prevented a failure or helped pass an inspection.
Keep it simple: Use checklists, photos, or drop-downs instead of freeform text fields.
One technician updating asset history on a mobile app after a service call is a win. Build from there.
7. Use Reporting to Show Value
Once your CMMS is running—even on just a few assets—you’ll quickly build a record of performance. Use simple reports to track:
Equipment downtime (before vs. after PM)
Frequency of unplanned vs. planned work
Maintenance costs over time
Time spent on each type of task
This lets you:
Prove ROI
Plan smarter
Get ahead of failures
You’ll no longer rely on guesswork—or the memory of the technician who just quit.
Keep It Light, Keep It Lean
Preventive maintenance doesn’t have to be an all-or-nothing effort. With a modern CMMS, even the smallest company can:
Reduce breakdowns
Extend asset life
Improve team productivity
Reduce costs over time
The key is to start small, choose the right tool, and keep the process simple.
You don’t need a full maintenance department or a big IT budget. You just need a commitment to consistency, and a platform that makes it easy for your team to follow through.
In 2025, preventive maintenance is no longer just best practice; it’s smart business. And now, it’s accessible.