Why Preventive Maintenance Reduces Asset Downtime and Boosts Efficiency

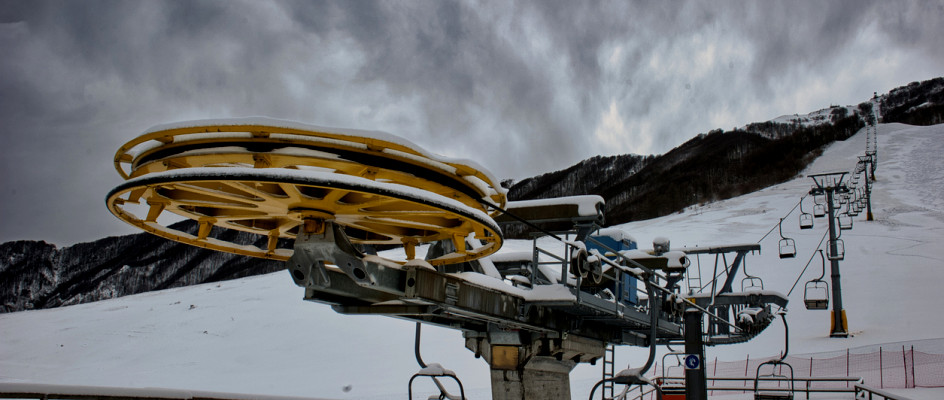
Preventive maintenance is a proactive approach to asset management that involves scheduled inspections, repairs, and upkeep to prevent equipment failures and unplanned downtime. This strategic maintenance methodology aims to identify and address potential issues before they escalate, ensuring that assets operate at peak efficiency. In this blog post, we will delve into the definition of preventive maintenance, explore its critical role in reducing asset downtime, and demonstrate why every business—large or small—should prioritize it.
What Is Preventive Maintenance?
Preventive maintenance (PM) is a systematic, planned approach to maintaining equipment and facilities. It involves regularly scheduled tasks such as inspections, servicing, and minor repairs with the primary objective of preventing unexpected breakdowns. The main idea is to catch and address small issues before they develop into significant problems that can disrupt operations.
Businesses across all industries—manufacturing, logistics, healthcare, education, and more—rely on assets that must operate reliably. PM helps safeguard these investments, extending their lifespan and minimizing operational interruptions.
Key Components of Preventive Maintenance
Effective preventive maintenance programs are built around several key components. Each contributes to minimizing downtime and ensuring that assets remain in top condition.
Scheduled Inspections
Regular inspections are the foundation of any successful preventive maintenance program. These are conducted at predefined intervals, allowing maintenance teams to catch early signs of wear and tear, misalignment, corrosion, or other indicators of potential failure. The frequency and depth of inspections depend on the asset type, usage intensity, and manufacturer’s guidelines.
By systematically reviewing assets before they fail, businesses can plan repairs at convenient times—eliminating unplanned stoppages that disrupt productivity.
Routine Lubrication
Mechanical systems rely heavily on lubrication to reduce friction between moving parts. Without proper lubrication, components wear faster, generate excess heat, and can fail prematurely. Preventive maintenance schedules typically include tailored lubrication tasks based on each machine’s specific needs.
This simple but essential practice keeps equipment running smoothly and helps prevent excessive wear and tear that could otherwise lead to sudden breakdowns.
Replacement of Wearable Parts
Components such as belts, bearings, filters, and seals are naturally prone to degradation over time. Preventive maintenance includes proactive replacement of these items before they wear out completely.
By replacing components on a schedule rather than waiting for failure, businesses reduce the likelihood of emergency repairs and expensive last-minute part sourcing. It also ensures consistent performance and avoids gaps in service.
Calibration and Alignment
Precision equipment must operate within narrow tolerances to function correctly. Misalignments or improper calibration can lead to reduced efficiency, errors, and ultimately equipment failure. Preventive maintenance includes routine calibration and alignment checks to ensure accuracy and consistency.
This is especially important in industries like manufacturing, where even slight deviations can affect product quality or increase operational costs.
Cleaning and Surface Treatments
Over time, dirt, dust, grime, and corrosive substances can accumulate on equipment surfaces, impacting performance and accelerating deterioration. Preventive maintenance programs include regular cleaning and, where necessary, surface treatments such as corrosion-resistant coatings or repainting.
Maintaining cleanliness not only keeps equipment in good working order but also improves workplace safety and aesthetics.
Software Updates and System Checks
Modern equipment often includes embedded software, automation systems, or IoT components. These require regular updates and diagnostic checks to ensure compatibility, security, and performance.
Preventive maintenance plans should incorporate routine software updates and system health checks to catch bugs, patch vulnerabilities, and ensure the digital infrastructure behind assets functions as intended.
The Role of Preventive Maintenance in Reducing Downtime
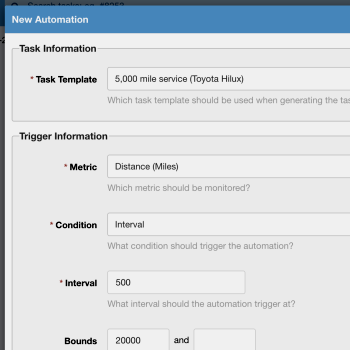
Unplanned downtime is costly. When a machine stops unexpectedly, it can bring entire operations to a halt. Labor costs go up, production timelines slip, customers become dissatisfied, and revenue is lost. Preventive maintenance directly addresses these risks by ensuring equipment is always operating at peak performance.
Here’s how preventive maintenance minimizes asset downtime:
Early Detection and Mitigation
Inspections and diagnostics built into preventive maintenance routines help identify small issues that, if left unchecked, could snowball into major failures. For example, detecting a slightly frayed belt early allows for timely replacement—avoiding the downtime caused by a snapped belt in mid-operation.
Scheduled Servicing, Not Emergency Repairs
One of the biggest advantages of preventive maintenance is that it allows organizations to plan servicing at non-disruptive times. This is far preferable to unpredictable breakdowns that occur during peak hours or crucial production cycles.
Consistent Performance and Efficiency
Properly maintained equipment runs more smoothly and predictably. Well-lubricated, calibrated, and cleaned machines not only perform better but also consume less energy and require less intervention, keeping productivity steady and costs low.
Safer Work Environment
Equipment failures can lead to safety hazards for operators and bystanders. Preventive maintenance ensures that safety features remain functional and equipment stays in safe operating condition. A safer workplace means fewer injuries, less downtime, and lower liability exposure.
Why Preventive Maintenance Matters for All Businesses
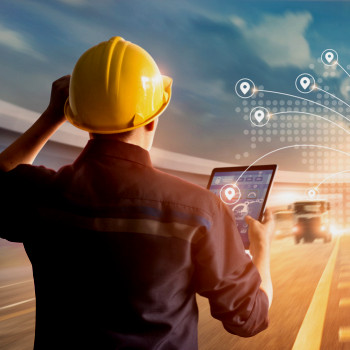
Regardless of your business size, PM delivers tangible benefits:
Lower repair costs – Fixing problems early avoids expensive overhauls.
Higher ROI on assets – Assets last longer and perform better.
Improved compliance – Regular checks ensure adherence to safety and quality regulations.
Happier teams – Maintenance staff spend less time putting out fires, and production teams experience fewer disruptions.
For small and mid-sized businesses, investing in preventive maintenance is especially critical. Limited resources make it all the more important to keep operations running smoothly. The costs of unexpected downtime can hit smaller operations much harder.
Leveraging CMMS for Preventive Maintenance
A Computerized Maintenance Management System (CMMS) can take your PM efforts to the next level. CMMS software simplifies the process of scheduling, tracking, and managing preventive maintenance. It ensures that nothing is missed and gives maintenance managers data-driven insights into equipment health and performance.
Key features of a CMMS include:
Automated reminders and task generation
Asset history tracking
Real-time status updates
Reporting and compliance logs
Mobile access for field teams
Implementing a CMMS helps eliminate guesswork and standardizes maintenance practices across your organization.
Maintainly CMMS for Reducing Asset Downtime
Preventive maintenance is much more than a maintenance strategy—it's a smart, cost-effective approach to managing your assets. By implementing a strong preventive maintenance program, businesses can reduce downtime, increase asset reliability, and create a safer, more efficient workplace.
Ultimately, preventive maintenance is an investment in your business’s long-term success. With the right tools, processes, and mindset, you can shift from reactive chaos to proactive control—and see the results in your bottom line.