The Maintenance Bathtub Curve: Understanding Asset Lifecycle Failure Patterns

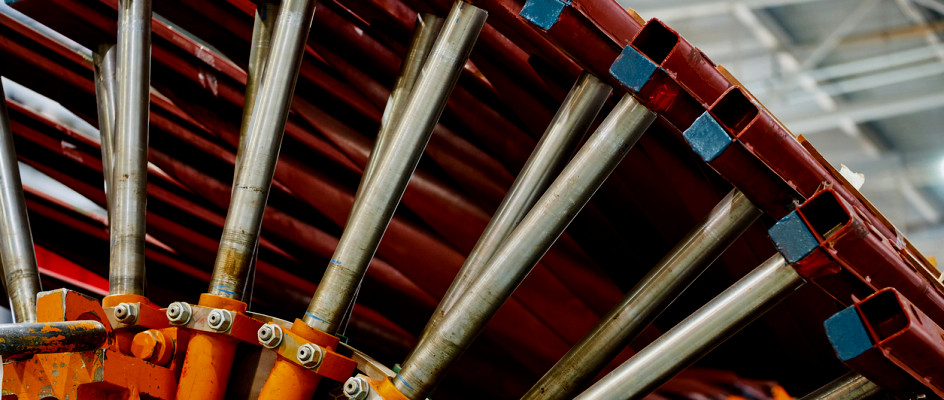
Few concepts are as foundational as the maintenance bathtub curve maintenance and reliability engineering. This powerful visual model illustrates how equipment failure rates typically evolve throughout an asset's lifecycle. Understanding this curve helps maintenance teams develop smarter strategies, optimize resources, and make data-driven decisions about when to repair, refurbish, or replace critical equipment.
Let's dive deeper into what the bathtub curve is, why it matters for your maintenance operations, and how you can leverage this knowledge to extend equipment life and reduce costly downtime.
What Is the Maintenance Bathtub Curve?
The maintenance bathtub curve is a graphical representation that plots failure rate against time for industrial assets. It gets its name from its distinctive shape that resembles a cross-section of a bathtub, high at both ends with a flat section in the middle. This curve isn't just theoretical; it's based on decades of observed failure patterns across numerous industries and equipment types.
The curve divides an asset's lifecycle into three distinct phases, each with unique characteristics and maintenance implications.
The Three Phases of the Bathtub Curve
1. Infant Mortality Phase (Early Failure Period)
Typically spanning the first few months of operation, this initial phase is characterized by a high failure rate that gradually decreases over time. The curve tends to be steeper for complex equipment and systems, often revealing design flaws or installation errors. This phase typically covers about 10-15% of the asset's expected lifespan.
Common Causes:
Manufacturing defects and quality issues
Improper installation or commissioning
Design flaws or material weaknesses
Inadequate start-up procedures
Misalignment or improper calibration
Consider a real-world example: A newly installed production line exhibits several stoppages and component failures in its first six weeks of operation. Investigation reveals that some bearings were incorrectly sized during manufacturing, while several sensors were improperly calibrated during installation.
During this phase, maintenance strategy should emphasize thorough acceptance testing and commissioning. Organizations should implement burn-in procedures before full deployment and conduct frequent inspections and vibration analysis during early operation. Close monitoring of operational parameters, detailed documentation of early failures for warranty claims, and training operators on proper equipment use are essential during this vulnerable period.
2. Normal Life Phase (Random Failure Period)
This phase represents the majority of an asset's operational life, often spanning 70-80% of its total lifespan. It's characterized by a low and relatively constant failure rate. Failures occur randomly rather than systematically, with equipment performing at designed efficiency levels. This longest phase of the asset lifecycle features relatively predictable maintenance requirements.
During normal operation, failures typically stem from random external factors like power surges or operator errors, occasional undetected manufacturing defects, environmental influences such as temperature fluctuations or contamination, normal stress variations during operation, and occasionally missed maintenance or inspection points.
A typical example would be a conveyor system that runs reliably for several years with only occasional, unpredictable failures. These rare stoppages are typically caused by random factors like power fluctuations or material jams rather than systematic issues with the equipment itself.
Recommended Maintenance Approaches:
Regular preventive maintenance schedules
Condition-based monitoring programs
Reliability-centred maintenance techniques
Statistical analysis of failure patterns
Optimization of spare parts inventory
Documentation of failure modes and effects
3. Wear-Out Phase (End-of-Life Failure Period)
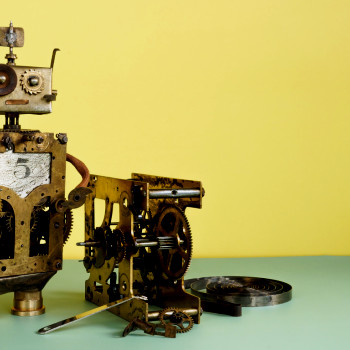
The final 10-20% of an asset's lifecycle is marked by a steadily increasing failure rate as components reach the end of their useful life. Organizations typically experience diminishing returns on maintenance investments, reduced overall equipment effectiveness, higher energy consumption for the same output, increased safety risks, compliance concerns, and a growing maintenance backlog.
Signs of Entering the Wear-Out Phase:
Increasing frequency of breakdowns
Longer repair times and parts delays
Rising maintenance costs
Decreased production efficiency
Growing energy consumption
More frequent quality issues
After 12 years of operation, for instance, a CNC machine might begin experiencing frequent breakdowns despite regular maintenance. Component failures become increasingly common, downtime extends, and replacement parts become harder to source as the manufacturer has released three newer models since installation.
During this challenging period, the maintenance strategy should shift toward increased inspection frequency and condition monitoring. Organizations need to conduct a cost-benefit analysis for major overhauls versus replacement and plan for technology upgrades or system replacement. Some equipment might be reallocated to less critical applications, while certain components might shift to a run-to-failure approach. Capital expenditure planning, budgeting for replacement, and knowledge transfer before equipment replacement become increasingly important.
How the Bathtub Curve Influences Maintenance Decisions
Understanding where your assets sit on the bathtub curve should directly influence your maintenance approach. This knowledge shapes key maintenance decisions throughout an asset's lifecycle in several important ways.
Maintenance Strategy by Phase
Infant Mortality Phase Strategies
During the early life of equipment, proactive quality control becomes essential. Organizations should implement rigorous vendor quality requirements, conduct thorough factory and site acceptance testing, and document baseline performance metrics to identify deviations quickly.
Key Focus Areas:
Enhanced monitoring with additional temporary sensors
Frequent inspections beyond manufacturer recommendations
Detailed failure documentation for warranty claims
Targeted training for operators and maintenance personnel
Clear communication channels with equipment suppliers
Documentation and warranty management take center stage during this phase. Maintaining detailed failure logs supports warranty claims, while establishing clear communication channels with equipment suppliers facilitates rapid response to early issues. Documenting all modifications and adjustments made during this period provides valuable information for future installations.
Normal Life Phase Strategies
As equipment enters its stable period, preventive maintenance optimization becomes the focus. Maintenance teams can fine-tune PM schedules based on actual equipment performance, implement reliability-centered maintenance analysis, and develop failure mode and effects analysis. This is also the ideal time to create standardized job plans for routine maintenance tasks.
Predictive technologies deliver significant value during this phase. Organizations typically deploy appropriate condition monitoring technologies, establish vibration analysis programs for rotating equipment, implement oil analysis for lubricated systems, and utilize thermography for electrical systems and connections.
Data Points to Track:
Mean time between failures (MTBF)
Overall equipment effectiveness (OEE)
Key performance indicators for maintenance
Failure modes and patterns
Energy consumption trends
Maintenance cost per operating hour
Continuous improvement initiatives thrive during this stable period. Conducting root cause analysis on significant failures helps prevent recurrence, while reliability improvement projects enhance overall performance. Standardizing best practices across similar equipment and developing operator-driven maintenance programs further extend equipment life.
Wear-Out Phase Strategies
As equipment ages, enhanced surveillance becomes necessary. Increasing inspection frequency for critical components and implementing additional condition monitoring points helps identify problems earlier. Monitoring for signs of diminishing performance and tracking increasing energy consumption provides early warning of impending failures.
Financial analysis takes on greater importance during the wear-out phase. Teams calculate remaining useful life estimations, perform maintenance versus replacement cost analysis, develop total cost of ownership models, and plan capital expenditure for inevitable replacement equipment.
Critical End-of-Life Considerations:
Increased safety and compliance risks
Availability of spare parts and technical support
Knowledge transfer for aging systems
Contingency planning for critical failures
Technology migration pathways
Production continuity during transitions
Risk management concerns intensify as equipment ages. Organizations must assess increased safety risks, review compliance with current regulations that may have changed since installation, develop contingency plans for critical equipment failure, and secure sources for increasingly obsolete replacement parts.
Practical Application: Creating a Phase-Based Maintenance Plan
Applying bathtub curve principles to your maintenance strategy requires identifying where each asset sits in its lifecycle. A practical approach begins with asset classification. Maintenance teams should categorize equipment by age relative to expected lifetime, use failure history to identify probable lifecycle phase, consider manufacturer obsolescence notices and support status, and review performance trend data for signs of wear-out.
Implementation Steps:
Classify all major assets by their lifecycle phase
Apply appropriate maintenance tactics for each phase
Document phase-specific requirements and indicators
Allocate resources according to lifecycle needs
Review and adjust classifications regularly
Phase-appropriate tactics follow this classification. Organizations should apply enhanced monitoring to new equipment while implementing reliability-centered strategies for midlife assets. Developing replacement planning for end-of-life equipment and adjusting spare parts stocking based on lifecycle phase ensures appropriate resource allocation.
Documentation requirements vary by phase as well. Creating phase-specific checklists for different lifecycle stages helps standardize approaches. Developing trigger points for strategy transitions, documenting key indicators that signal phase changes, and maintaining historical data improves future lifecycle predictions and planning accuracy.
Beyond the Basic Curve: Advanced Considerations
While the standard bathtub curve provides an excellent foundation, maintenance professionals should be aware of several important nuances that affect real-world applications.
Modified Bathtub Curves
Not all equipment follows the classic bathtub pattern. Equipment can exhibit variations that maintenance teams should recognize and plan for. Electronic components, for instance, often show high early failure rates but may not exhibit increased end-of-life failures before obsolescence makes them irrelevant, creating an "Infant Mortality Only" curve pattern.
Common Variations:
"Infant Mortality Only" Curve (common in electronics)
"No Infant Mortality" Curve (highly tested components)
"Multiple Mortality" Curve (systems with major overhauls)
"Gradual Wear-Out" Curve (mechanical components)
"Sudden Death" Curve (catastrophic failure modes)
Highly tested and burned-in components may skip the early failure phase entirely and begin life in the normal operations zone, displaying a "No Infant Mortality" curve that starts flat and only rises at end-of-life. Complex systems that undergo major overhauls may experience multiple mini-bathtub curves throughout their lifecycle, with failure rates temporarily increasing after each refurbishment before settling into another stable period.
Industry-Specific Considerations
The bathtub curve manifests differently across industries, reflecting the unique characteristics of different operating environments. Process industries typically see longer normal operation phases with more gradual wear-out slopes. The significant impact of corrosion and erosion creates unique failure patterns, and maintenance is often tied to scheduled turnarounds rather than equipment condition alone.
Discrete manufacturing environments generally experience shorter equipment lifecycles with more pronounced wear-out phases. The greater impact of technological obsolescence accelerates replacement decisions, and maintenance must often be balanced against production demands that may limit access to equipment.
Facility equipment follows yet another pattern, with extended normal operation phases and slower wear-out progression. Significant seasonal variations affect failure patterns, and maintenance is often combined with energy efficiency initiatives that may extend useful life through reduced operational stress.
Using Data to Refine Your Curve
Modern maintenance organizations can go beyond theoretical curves to develop equipment-specific failure profiles that guide more precise decision-making. Failure history analysis forms the foundation of this approach, with maintenance teams plotting actual failure rates against time for equipment classes. Identifying specific failure modes associated with each phase and calculating average phase durations for similar equipment creates a more accurate picture than generic models.
Data-Driven Enhancement Techniques:
Historical failure analysis and pattern recognition
Machine learning for early phase transition detection
Digital twin simulation of asset aging
Predictive algorithms for remaining useful life
Statistical analysis of failure distributions
Condition-based monitoring trend analysis
Predictive analytics takes this refinement further, using machine learning to identify early indicators of phase transitions that may not be obvious to human observers. Developing algorithms to predict remaining useful life and creating dashboards showing asset position on lifecycle curves helps maintenance planners make more informed decisions about resource allocation and replacement timing.
Leveraging the Bathtub Curve for Maintenance Excellence
The maintenance bathtub curve isn't just a theoretical concept—it's a practical framework that should inform your entire maintenance strategy. By understanding and applying this model, maintenance teams can allocate resources more effectively across the equipment lifecycle, anticipate and mitigate failure risks at each phase, make data-driven decisions about repair versus replacement, optimize maintenance budgets and capital expenditure timing, and improve overall equipment reliability and plant performance.
Key Benefits of Lifecycle-Based Maintenance:
Enhanced reliability and uptime
Optimized maintenance resource allocation
Better capital planning and budgeting
Reduced emergency repairs and downtime
Extended asset life and improved ROI
More strategic decision-making
Remember that each phase requires different approaches, tools, and mindsets. By tailoring your maintenance strategy to the specific needs of each lifecycle stage, you can maximize asset performance, extend equipment life, and minimize the total cost of ownership.
Most importantly, the bathtub curve reminds us that maintenance isn't a one-size-fits-all proposition. Equipment needs evolve over time, and so should your approach to caring for it. By aligning your maintenance strategy with these natural lifecycle phases, you'll be well-positioned to achieve maintenance excellence across your entire operation.
Want to learn more about optimizing your maintenance strategy? Get in touch to discuss your maintenance use case, or start a free 14-day trial today.