Keeping the Lights On: Work Order Fix Management in the Energy Sector

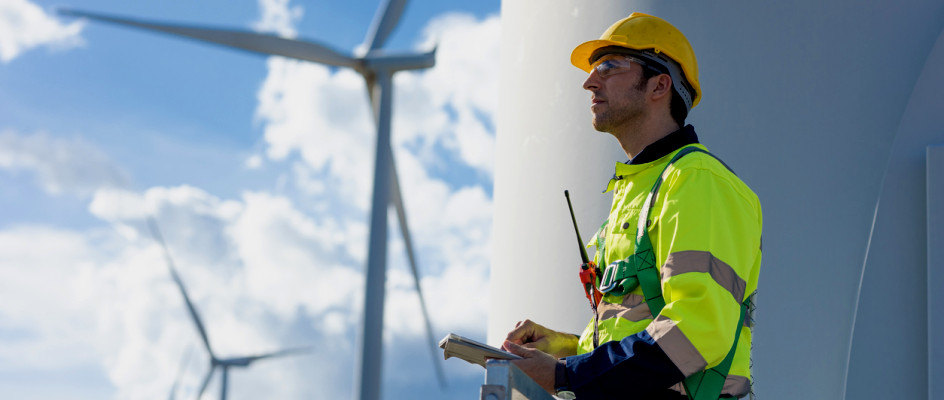
Maintenance Management for the Energy Sector
The energy sector is the backbone of modern society, and ensuring its smooth operation is paramount. As the world's reliance on energy grows, so does the need for effective work order fix management. A proactive approach is critical in this realm to ensure that lights remain on, machinery functions optimally, and industries don't face unnecessary downtimes. Here, we delve deeper into the significance, processes, and best practices of work order fix management in the energy sector.
The Significance of Work Order Fix Management in the Energy Sector
The energy sector is an intricate web of systems, equipment, and operations that work cohesively to ensure power reaches every household and industry. Within this framework, the role of work order fix management emerges as paramount. Its significance stems from ensuring operational fluidity and preventing potential cascading failures that can ripple across interconnected energy systems.
Curtailing Operational Downtimes
In the bustling realm of the energy sector, time truly equates to power. When equipment falters, even momentarily, it can lead to bottlenecks, disrupting the supply chain. Effective work order fix management is the antidote to such disruptions. By promptly addressing and rectifying maintenance requests, this system ensures:
Continuous Power Supply: We minimize downtimes to ensure uninterrupted power distribution to homes, businesses, and critical infrastructure.
Operational Efficiency: Regular maintenance checks and swift addressing of issues mean that power plants and energy facilities operate at their optimum capacity without any unexpected halts.
Championing Safety Protocols
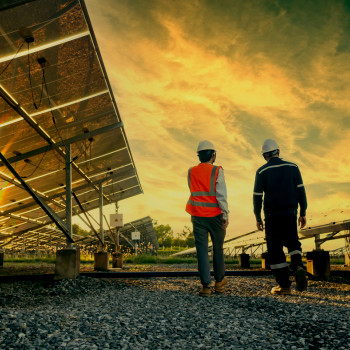
The energy sector, given its nature, is fraught with risks. Equipment malfunctions, system failures, or even minor glitches can escalate rapidly into safety hazards. Here's where work order fix management plays a crucial role:
Preventative Approach: By addressing issues promptly, we prevent potential accidents resulting from these malfunctions. It's not just about reactive measures but about foreseeing potential pitfalls and addressing them preemptively.
Safeguarding Assets and Personnel: Performing timely maintenance checks and promptly addressing reported issues ensures the safeguarding of both machinery and personnel operating them against potential hazards.
Ensuring Fiscal Efficiency through Proactive Maintenance
Every breakdown or malfunction carries with it a financial implication. The ramifications are multifaceted, whether it's the cost of emergency repairs, the replacement of parts, or the larger impact of operational halts on the energy market. Preventative work order fix management is a boon in terms of fiscal planning for several reasons:
Preventing Major Breakdowns: By addressing minor issues promptly, the system prevents them from escalating into major, cost-intensive breakdowns.
Extending Equipment Lifespan: Regular maintenance, guided by effective work order management, ensures that equipment performs optimally and lasts longer, reducing replacement costs in the long run.
Efficient Resource Allocation: With a streamlined work order system, human and material resources are managed judiciously, ensuring maximum returns on investment.
Processes in Work Order Fix Management
A meticulous understanding of work order fix management is vital to maximize efficiency and address maintenance challenges. By dissecting each step, we can uncover the nuances that make this process essential in the energy sector:
1. Initiation: The First Step to Problem Resolution
The initiation phase is the linchpin of effective work order management. Before taking any action:
Detailed Diagnosis: The issue at hand undergoes a comprehensive examination. This evaluation helps pinpoint the cause, gauge the severity, and forecast the potential ramifications of the problem. Not only does this step aid in determining the kind of attention the issue demands, but it also lays the foundation for subsequent stages.
Documentation is Key: Properly recording the identified issue is imperative. This practice includes capturing the date, time, machine or system involved, personnel on duty, and any immediate actions taken. A well-documented initiation can streamline the later stages of the process.
2. Prioritization: Deciphering the Urgency
In bustling energy facilities, the volume of tasks can be overwhelming. Hence, determining the urgency of each work order is pivotal:
Risk Analysis: Prioritization heavily relies on understanding the risks involved. Issues that compromise safety or the core functionality of the facility necessitate immediate attention.
Business Impact: Beyond immediate safety concerns, the business impact of an unresolved issue, such as potential downtimes, customer dissatisfaction, or revenue loss, also plays a significant role in prioritization.
3. Assignment: Getting the Right Hands on Deck
Once the problem is classified based on its urgency, the next step is to delegate the task:
Team or Individual Selection: Depending on the intricacy and nature of the issue, the task is assigned either to a team or an individual. This decision often hinges on the expertise required, the scope of the problem, and available personnel.
Matching Expertise: Matching the problem with someone with relevant experience and skills is essential. For example, if there is a problem with a turbine, it would be directed to specialists who deal specifically with turbines.
4. Execution: Putting Plans into Action
This process is where the rubber meets the road. The execution phase breathes life into the solution:
Rectification Methods: Depending on the issue's nature, the execution might involve repairing faulty parts, replacing components that are beyond repair, or even upgrading systems for better functionality and longevity.
Ensuring Compliance: As the energy sector is highly regulated, all actions should comply with industry standards and safety protocols.
5. Verification: Double-Checking the Solution
After the execution, an essential step is to ascertain that the solution works:
Functionality Test: Testing the repaired or replaced components to ensure they function as expected without any hitches.
Recurrence Prevention: An essential aspect of verification is ensuring that the solution addresses the present issue and forestalls similar problems in the future.
6. Closure: Sealing the Deal
The closure phase marks the end of the work order process:
Final Documentation: We thoroughly document all actions, replacements of parts, individuals involved, and the time taken. This documentation serves as a reference for addressing future similar issues and facilitates audits and compliance checks.
Feedback Loop: Before completely closing off, gathering feedback is beneficial. Understanding what went well and what challenges were faced can help refine the work order fix management process for future tasks.
7. Feedback: The Unsung Hero of Continuous Improvement
After the closure of a work order, the process doesn't end. Feedback plays a pivotal role in refining and optimizing future work order management:
Gathering Insights: Inviting feedback from the team members involved provides an opportunity to unearth potential inefficiencies or challenges they face during the process.
Adjustments and Refinements: Using this feedback, companies can make necessary adjustments to the process, tools, or even training methodologies. These iterative improvements elevate the efficacy of work order fix management over time.
8. Periodic Review: Keeping the Process Updated
The dynamic nature of the energy sector and technological advancements necessitates periodic reviews of the work order fix management process:
Benchmarking: Regularly comparing the company's practices with the industry's best standards can provide insights into areas of potential improvement.
Embracing Technological Evolution: As technology evolves, newer tools and software can make work order management even more efficient. Staying updated and incorporating these can significantly bolster the process.
9. Training: Equipping the Team for Success
An effective work order fix management process is as good as the team executing it. Regular training ensures:
Skill Enhancement: As the energy sector innovates, new challenges arise. Training effectively equips the team to tackle these novel challenges.
Uniformity in Approach: Regular training sessions ensure the entire team is aligned in their approach, ensuring consistency in work order execution across the board.
10. Data Analytics: The Power of Informed Decisions
In the age of digital transformation, leveraging data analytics can be a game-changer for work order fix management:
Predictive Maintenance: By utilizing data analytics, organizations can predict potential issues before they escalate into significant problems, enabling them to perform proactive maintenance.
Efficiency Tracking: Analyzing data from completed work orders can offer insights into areas where we can expedite the process or allocate resources more efficiently.
Harnessing the Power of Efficient Work Order Management in the Energy Sector
'Keeping the Lights On' is not just a metaphorical statement but a reflection of the unwavering commitment of the energy sector towards operational excellence. As our energy dependence continues to burgeon, the marriage of technology with an effective work order fix management process will undeniably shape the future of consistent and reliable energy delivery.
Incorporating tools like Fixed Asset Management further bolsters the efficacy of these processes. By embracing technological advancements and continually updating skills through training, the energy sector stands better equipped to tackle future challenges. With its predictive power, data analytics can position energy providers ahead of potential pitfalls.
The intricacies and demands of the energy sector are unparalleled, dictating a critical need for impeccable work order fix management. As the backbone of modern infrastructure, ensuring a steady and reliable supply of power to homes, industries, and critical facilities rests largely on the shoulders of a robust work order system.