Work Order Tracking Streamlines Operations

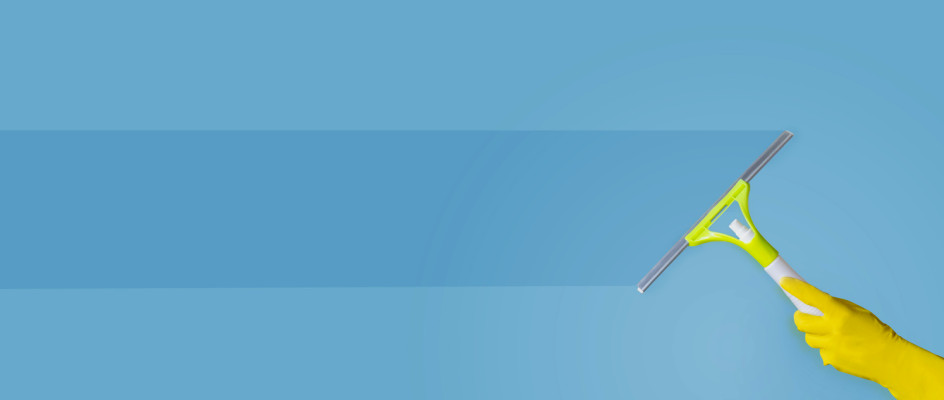
Work orders are essential for setting clear directives regarding actions, resources, and timelines for completing tasks. When work orders lack resources or clarity, it can be detrimental to your company’s workflow operations and possibly, revenue. If you’ve been managing work orders manually through Excel or outdated digital applications, it might be time for an upgrade.
A maintenance management system can help automate the work order process and streamline your operations. Here’s how Maintainly software can help you improve your processes.
What is Work Order Tracking?
Work orders involve identifying a specific task, the people required to execute and all equipment and tools needed along with a timeline. While work orders vary by industry, they are valuable because they highlight critical production information and help track the progress of any employee's workload.
Work orders are usually submitted in person to a manager or foreman or through company-specific data management systems. Work orders can easily get lost in complex daily workloads, leading to service delays and significant revenue loss.
Work order tracking solves this problem by providing a system to track all ongoing work orders through a simplified interface. These tracking systems generate order IDs, descriptions, request dates, the current status of the order, and all other necessary information at your fingertips. It’s a system commonly used in maintenance management software applications (CMMS) to help companies improve their productivity and efficiency in their line of work.
The Benefits of Work Order Tracking
Tracking work orders via CMMS offers many ways to streamline operations and boost productivity, providing opportunities for growth. When you're managing a large volume of orders, a good system can provide better resources by:
Standardizing Workflows: All work orders can be standardized within one system. This system eliminates unnecessary paperwork and gives you a centralized hub to schedule, assign, and complete work orders successfully. A standardized system also allows you to detail orders, estimate costs, and manage assets more effectively.
Real-Time Monitoring: Work orders that aren’t properly managed can often result in revenue loss, and through systems that use work order tracking, you can monitor the progress of your work order in real time. By doing so, you can track performance metrics for equipment downtime and costs associated with performed work and monitor assets so that your tasks can get done on time within your budget.
Better Communication: One of the biggest problems most companies face with work orders is communication. When work orders cannot be resolved immediately, it’s often due to problems understanding the work order’s details and priority. A work order tracking system can help ease communication issues and ensure that tasks with higher priority get done faster.
Delegate Maintenance: Handling streams of work orders and manually setting their priorities can be costly and stressful, especially when work orders that require immediate attention lack the emphasis they need to get done. Work order tracking can help establish priorities for inspections, emergency maintenance orders, and corrective measures and help instil a better system for creating preventative maintenance orders that help save on costs.
Improved Efficiency: Most of all, work order tracking is an efficient system that streamlines all your operations, helping you save on costs, assists in inventory management, and reduces downtime for increased productivity. You can track work orders in real time and improve data communication, speeding up your workflow.
How CMMS Improves Work Order Flow
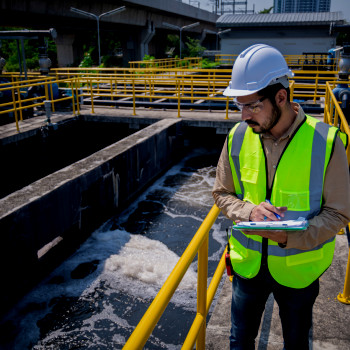
While work order tracking is effective, it is most effective when part of a complete system. When combined with other features such as location tracking, automated task scheduling, and even preventative data analysis measures it can drastically reduce production costs.
At Maintainly, our CMMS software includes work order tracking applications alongside features such as inventory management, asset location tracking, timesheets, and a long list of features designed to not only streamline and focus the maintenance team, but to do so using industry best-practices. Our CMMS software provides an intuitive, simple-to-use interface that reduces the traditional requirement for a lot of CMMS training. Plus, with modifiable, flexible plans and add-ons, there's no more navigating through a giant CMMS when you're only using a fraction of the product.
Through Maintainly, you can easily reduce equipment downtime, schedule maintenance repairs, and automate your work orders using task template and automations on assets.
Get Smarter Work Order Tracking with Maintainly Today!
Create, submit, and track your order’s life cycle with ease. Maintainly CMMS software allows management and key stakeholders to produce accurate overviews of all your company’s maintenance needs. Imagine getting asked an important question by the CEO and in 20 seconds producing unlimited work order placement, data report generation, automated asset and data analysis, work audit trail tracking, and more.
If you want to learn more about our CMMS software and what it can offer you, discover Maintanly and start your free trial with us today!