How Does CMMS Help with Predictive Maintenance in Manufacturing?

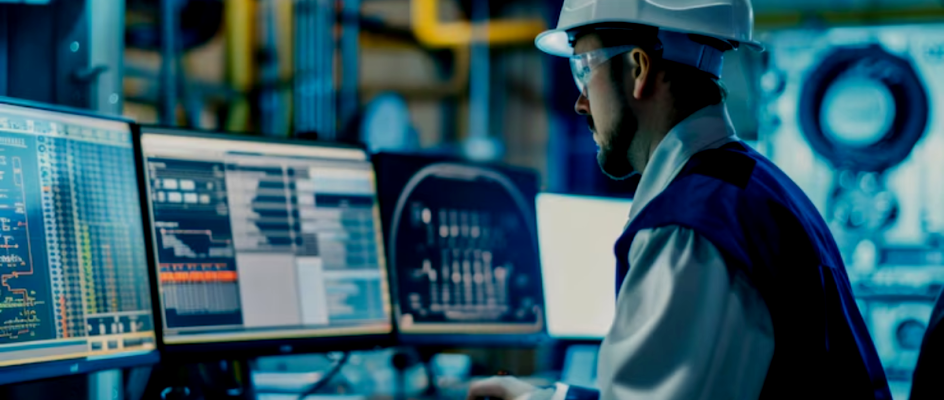
Predictive maintenance is a strategy that uses data analytics, machine learning, and sensors to monitor equipment conditions and predict potential failures. Unlike preventive maintenance, which follows a fixed schedule regardless of the actual condition of machinery, predictive maintenance only triggers maintenance actions when data indicates that failure is imminent.
Technologies such as vibration analysis, thermal imaging, ultrasonic testing, and oil analysis are often used to gather critical equipment data. By continuously analyzing performance metrics and data, it can identify subtle warning signs of wear or malfunction long before a failure occurs. This approach allows manufacturers to repair or replace components before any breakdown, ultimately saving time and money.
Manufacturing equipment is expensive and is meant to last for several years. Even with a generous budget, replacing equipment is costly and disruptive. This is where a Computerized Maintenance Management System comes into play. In this comprehensive guide, we will explain the role of CMMS in predictive maintenance.
What Is a CMMS?
A Computerized Maintenance Management System (CMMS) is a software platform that helps organizations manage maintenance operations more efficiently. It centralizes data, automates maintenance scheduling, generates work orders, tracks equipment history, and provides actionable insights through reports and dashboards.
When integrated with predictive maintenance technologies, a CMMS becomes a powerful tool that bridges the gap between data collection and actionable maintenance execution.
For better understanding, let’s take an example. Consider a manufacturing plant that utilises heavy machinery operating continuously, 24 hours a day. With a CMMS connected to IoT sensors, the maintenance team receives alerts when a machine’s vibration levels exceed safe thresholds. Instead of waiting for the machine to fail, a technician is dispatched to inspect and resolve the issue before it causes a breakdown. Not only is downtime avoided, but the equipment also continues to perform reliably, extending its service life.
The Role of CMMS in Predictive Maintenance
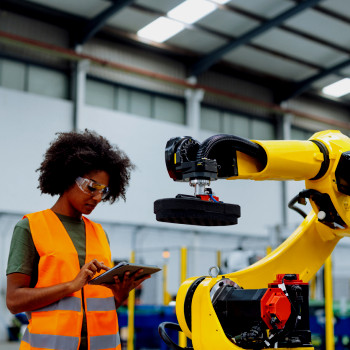
Here are six key ways in which CMMS supports predictive maintenance in manufacturing:
1. Real-Time Data Integration
One of the most transformative features of a CMMS is its ability to integrate with Internet of Things (IoT) devices and condition-monitoring sensors that are installed on manufacturing equipment. These devices collect real-time data on a variety of key indicators—such as temperature, vibration, pressure, and run-time hours.
Rather than manually analyzing raw sensor data, the CMMS centralizes and processes this information, converting it into actionable insights through intuitive dashboards and automated alerts. Maintenance teams can track equipment performance across multiple locations, detect patterns of degradation, and receive early warnings about abnormal conditions.
This allows technicians to respond quickly and proactively, minimizing the risk of equipment failure and ensuring production lines stay operational. With real-time integration, maintenance becomes smarter and more responsive.
2. Automated Work Order Generation
Traditionally, maintenance teams relied on scheduled inspections or reactive responses to breakdowns. But with a CMMS powered by predictive maintenance, the process becomes automated and intelligent.
When the system detects an anomaly—like an unusual vibration signature or a sharp increase in motor temperature—it can automatically generate a work order. This order is then assigned to the appropriate technician based on skillset, availability, and urgency. No manual intervention is needed.
This automation ensures a rapid response, reduces human error, and prevents issues from escalating into costly failures. In environments where time is money, this capability can deliver significant operational and financial advantages.
3. Maintenance Scheduling Based on Equipment Condition
Predictive maintenance shifts the paradigm from calendar-based scheduling to condition-based maintenance. Instead of servicing machines based on arbitrary time intervals, a CMMS enables maintenance to occur only when the data indicates a need.
This not only avoids unnecessary maintenance—saving time and labor—but also ensures that critical issues are not overlooked. By servicing equipment at the optimal time, manufacturers can extend asset life, improve reliability, and maintain consistent production output.
Moreover, this data-driven scheduling helps reduce over-maintenance, which can lead to unnecessary wear and tear, as well as under-maintenance, which increases the risk of unexpected breakdowns. The result is a well-balanced maintenance strategy that aligns with the actual health of the equipment.
4. Centralized Asset Data and Maintenance History
A CMMS acts as a single source of truth for all asset-related information. Every machine, component, and tool has its own digital record, which includes:
Service and repair history
Inspection logs
Downtime events
Parts replaced
Technician notes
Manufacturer guidelines
When a predictive maintenance alert is triggered, technicians can instantly access this data to understand the context. For instance, if a motor begins to overheat, the technician can review past work orders to see if a similar issue occurred, what was done, and whether replacement parts were involved.
This historical visibility enables better decision-making, faster diagnosis, and more effective repairs. It also supports compliance and audits by maintaining a comprehensive, searchable maintenance record.
5. Improved Resource Allocation
Managing resources—technicians, tools, spare parts, and time—is one of the most challenging aspects of industrial maintenance. A CMMS brings clarity and coordination to this process.
When a potential failure is identified, the CMMS helps maintenance managers:
Match the task with the most qualified technician
Check inventory levels for needed spare parts
Identify available time slots in the production schedule
Ensure safety protocols and equipment access are in place
This holistic view ensures that every maintenance activity is executed efficiently, without delays or disruptions to operations. Predictive maintenance becomes not just about spotting problems early, but also about responding in a well-organized, resource-efficient manner.
6. Reduced Downtime and Cost Savings
Ultimately, the goal of predictive maintenance is to minimize unplanned downtime, and a CMMS is key to making that a reality. By identifying and addressing potential failures before they happen, manufacturers can avoid costly production stoppages.
This proactive approach also leads to long-term cost savings:
Fewer emergency repairs
Lower labor costs due to better scheduling
Reduced spare parts consumption
Extended equipment life
Higher overall equipment effectiveness (OEE)
Additionally, predictable maintenance patterns improve budgeting and planning, giving plant managers greater control over operational expenses. The cumulative impact is a more resilient, efficient, and profitable manufacturing operation.
CMMS & Manufacturing
Predictive maintenance is no longer a futuristic concept, it's an essential component of modern manufacturing. When paired with a robust CMMS, it delivers unmatched visibility, control, and efficiency. From real-time monitoring to automated work orders and intelligent scheduling, a CMMS transforms data into action and uncertainty into confidence.
As the manufacturing industry continues to embrace digital transformation, investing in a CMMS with predictive maintenance capabilities isn’t just a smart move, it’s a strategic imperative.
If you are looking for the right CMMS software, try Maintainly. This is a modern CMMS that comes with great and reliable features you’ll love.