Maintainly Enhances Material Management with QR Code Integration

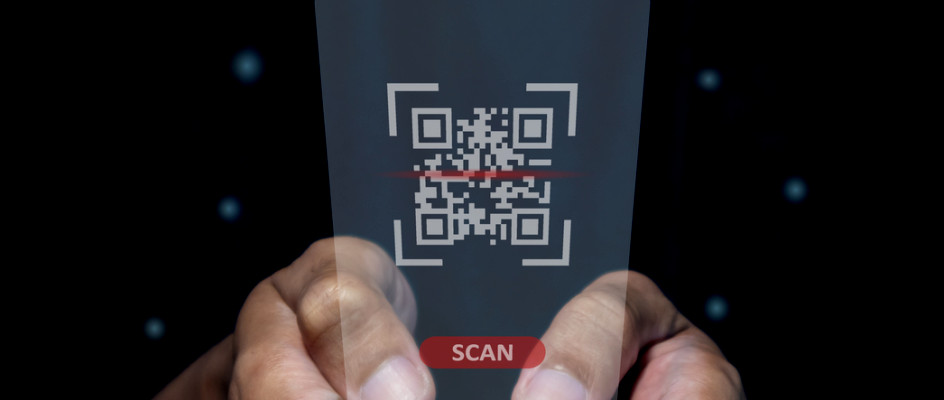
Maintainly has upgraded its material management system, transitioning from barcodes to QR codes for all materials (spare parts and consumables). This update expands functionality and improves user experience.
Key changes include:
Replacement of barcodes with QR codes for all materials
Implementation of a more secure and user-friendly material code system, utilizing entropy for enhanced security
Ability to print QR labels for individual materials or warehouse shelves
Integration with the Maintainly mobile app, allowing direct QR code scanning within tasks to track material consumption
These improvements build upon our previous barcode system, which already offered benefits such as inventory list filtering. The new QR-based system provides greater versatility and efficiency in material management.
For more information on the security improvements and the concept of entropy in coding, please visit our previous article on this subject.
Printing QR Labels for Inventory
QR labels in Maintainly can now be produced from multiple places:
Materials list page
Individual material page
Inventory orders
Consume Materials by Scanning the QR Label
Whether you're using the Maintainly CMMS iOS app or Android app, adding spare parts and consumables to a work order is as quick as pointing the camera at the material QR label.
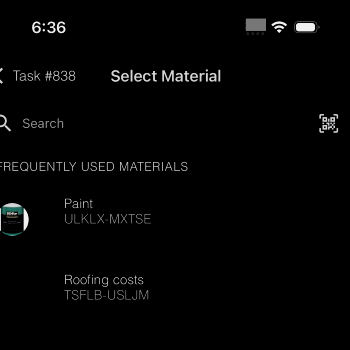
Follow these steps to add materials to a task:
Navigate to the appropriate task;
Click Materials in the left side menu;
Click the QR icon that's located in the search bar. Note that at this stage, it may be necessary to give Maintainly permission to access your phone's camera;
Hold the camera up to the QR label to scan;
Nominate the quantity consumed and then click Save.
QR Labels are an Essential CMMS Tool
QR labels have revolutionized inventory management, particularly in streamlining processes for technicians. The primary advantage lies in their ability to simplify and expedite the tracking of spare parts usage. Instead of manually searching through extensive lists or navigating complex filtering systems, technicians can now simply scan the QR code of a part they're using. This quick scan immediately records the part's usage, updates inventory levels, and associates the part with the specific task or work order.
This streamlined approach significantly reduces the time and effort required for inventory management tasks. Technicians no longer need to memorize part numbers or spend valuable time scrolling through digital catalogs. The scan-and-go method minimizes errors in reporting, ensures real-time inventory updates, and allows technicians to focus more on their primary repair and maintenance duties. Moreover, this efficiency translates to more accurate stock level tracking, improved reordering processes, and ultimately, a more responsive and cost-effective inventory management system. By simplifying the interaction between technicians and the inventory system, QR labels not only enhance productivity but also contribute to more precise usage data, enabling better forecasting and optimization of spare parts inventory.
For more information, visit Maintainly or check out our feature Help content.