Unlocking Performance: How Internal KPIs and CMMS Transform Asset-Intensive Organizations

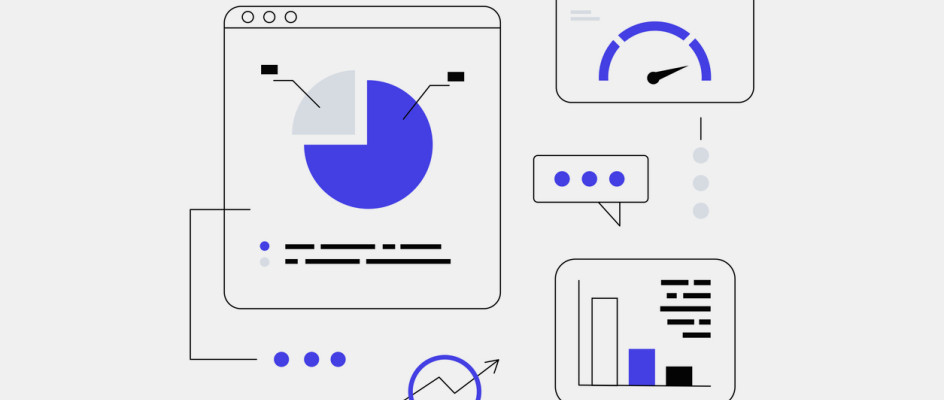
In asset-intensive industries - manufacturing, facilities management, utilities, logistics, and more - the performance of physical assets can make or break an organization’s ability to deliver value. When machines break down, vehicles sit idle, or equipment is mismanaged, productivity slows and costs rise. To manage this complexity, organizations need clear insights into how well their internal processes are functioning. That’s where internal performance KPIs come into play.
By focusing on the right metrics and leveraging the right tools, prticularly a Computerized Maintenance Management System (CMMS), organizations can turn maintenance into a strategic advantage rather than a cost center. This article explores how internal KPIs support performance, the role of a CMMS in tracking and improving them, and the measurable benefits that follow.
The Importance of Internal KPIs in Asset Management
Key Performance Indicators (KPIs) are essential for making sense of what’s happening inside maintenance and operations teams. Unlike external-facing metrics, like revenue or customer satisfaction, internal KPIs focus on operational efficiency, resource utilization, and asset reliability.
For organizations with large volumes of physical assets, KPIs provide early signals of inefficiencies, looming equipment failures, or maintenance overload. They also help identify patterns: Are certain machines breaking down more often? Are work orders consistently delayed? Are technicians overburdened or underused? With this level of insight, teams can take proactive steps to address issues before they escalate.
For example, tracking Mean Time Between Failures (MTBF) shows how reliably equipment is performing. If MTBF is falling over time, it may indicate that preventive maintenance is being skipped or that equipment is reaching the end of its usable life. Similarly, Mean Time to Repair (MTTR) can reveal whether your maintenance team has the right tools, procedures, and spare parts to respond efficiently to breakdowns.
Without tracking these types of metrics, organizations are left guessing, or worse, reacting only after major disruptions.
Moving from Reactive to Proactive with a CMMS
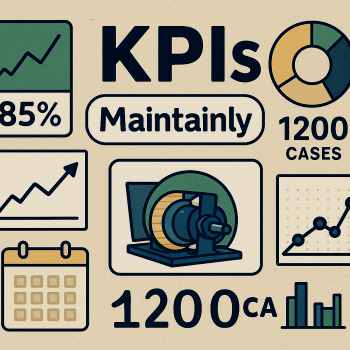
Despite the value of internal KPIs, many organizations struggle to track them consistently. Information might live in spreadsheets, emails, or be scattered across departments. Work orders are paper-based, or preventive tasks are manually scheduled and easily missed. This makes it difficult to measure performance accurately, let alone improve it.
This is where a CMMS becomes essential. A modern CMMS acts as a central command hub for maintenance operations. It allows organizations to automate preventive maintenance, track asset history, generate reports, and manage work orders from a single platform.
One of the most transformative benefits of a CMMS is the shift from reactive to proactive maintenance. Instead of waiting for assets to fail, teams can schedule maintenance based on usage thresholds, time intervals, or sensor data. By increasing the ratio of planned to unplanned work, organizations reduce emergency repairs, increase asset availability, and lower costs.
This shift is directly reflected in internal KPIs. For example, the Planned Maintenance Percentage (PMP) becomes a key indicator of maturity. A high PMP, say, 80% of maintenance tasks being planned, indicates a proactive culture where surprises are minimized. A low PMP suggests firefighting still dominates the workflow.
Managing Workflows, Not Just Work Orders
Beyond scheduling and automation, a CMMS enhances visibility and accountability across the maintenance function. With every work order logged digitally, maintenance managers can monitor task completion rates, identify backlog trends, and understand how long tasks take from initiation to closure.
This matters because time is money. Delayed or incomplete work orders can contribute to production losses, safety risks, or warranty violations. With a CMMS, managers can prioritize critical tasks, reassign overdue work, and even see which technicians are consistently meeting (or missing) performance benchmarks.
Technician utilization is another KPI that benefits from CMMS data. When time tracking is built into work orders, it's possible to distinguish between wrench time and admin time. This highlights inefficiencies, like time spent waiting for parts or searching for documentation, that can be streamlined through better planning or mobile access.
Cost Visibility and Smarter Budgeting
A key advantage of using a CMMS is that it ties operational activities to financial outcomes. Maintenance costs can be broken down by asset, site, or department, making it easier to pinpoint where money is being spent and whether that spend is delivering value.
For instance, if a particular machine consistently incurs high maintenance costs, the data from the CMMS can support decisions about whether to replace it, renegotiate vendor contracts, or invest in operator training. Similarly, tracking inventory usage through the system improves spare parts management. When you know which parts are frequently used, which are obsolete, and which are causing downtime due to stockouts, you can optimize your purchasing and reduce waste.
This level of cost transparency also supports long-term capital planning. Instead of relying on guesswork, organizations can use historical maintenance and performance data to forecast asset lifespan, budget more accurately, and make stronger business cases for upgrades.
Safety, Compliance, and Audit Readiness
In regulated industries, internal KPIs aren’t just about efficiency; they’re about compliance. Organizations need to prove that inspections, repairs, and calibrations are being done on time and according to standard operating procedures. A CMMS provides the audit trail needed to demonstrate this.
For example, if a regulator asks for proof that a safety valve was inspected last quarter, the CMMS can produce a timestamped work order, technician notes, and even photos. This reduces the administrative burden of audits and ensures that nothing slips through the cracks.
From a KPI perspective, tracking on-time completion of safety-critical tasks is essential. Missed inspections or skipped PMs can quickly erode trust and increase liability. The CMMS provides visibility into these leading indicators before they turn into lagging consequences.
Turning Data Into Decisions
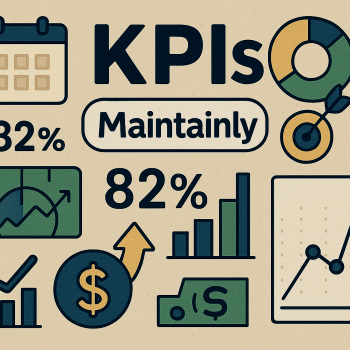
All the features of a CMMS, automated scheduling, asset tracking, real-time reporting, ultimately support one goal: better decision-making. By consolidating data and visualizing KPIs in dashboards or reports, organizations can see what’s working, what’s not, and what needs to change.
Leaders can compare performance across sites, identify trends over time, and align maintenance strategies with business goals. Are we improving MTTR quarter over quarter? Is our downtime decreasing as planned? Are our assets costing more to maintain as they age? With a CMMS, these questions are easier to answer, and act on.
Moreover, many CMMS platforms now offer integrations with IoT sensors and predictive analytics, pushing capabilities even further. This allows for condition-based maintenance, anomaly detection, and AI-driven insights, all of which enhance KPI accuracy and decision-making power.
Building a Culture of Continuous Improvement
Perhaps the most lasting benefit of combining internal KPIs with a CMMS is cultural. Maintenance teams that are empowered with data, supported by technology, and aligned with strategic objectives are more likely to embrace continuous improvement.
Technicians take pride in hitting performance targets. Managers spend less time chasing paperwork and more time optimizing workflows. Leadership gains confidence in the reliability of operations, and the entire organization benefits from smoother, more predictable performance.
In this environment, KPIs aren’t just numbers on a dashboard; they become part of a shared language of accountability and growth.
KPI's in Daily Processes
Organizations that maintain physical assets can’t afford to manage them blindly. Internal performance KPIs offer a clear lens into the health of operations, while a CMMS provides the platform needed to act on that insight.
By implementing a CMMS and embedding KPI tracking into daily processes, organizations gain the ability to reduce downtime, control costs, improve compliance, and make smarter decisions. More importantly, they build a foundation for resilience, adaptability, and long-term performance.
In a world where every minute of uptime counts, the ability to manage maintenance intelligently is no longer optional; it’s a competitive edge.
Need help choosing the right CMMS or defining your internal maintenance KPIs? Reach out to our team of maintenance experts for a consultation and learn how to unlock the full potential of your asset management strategy. Or start a 14-day trial of Maintainly today.