Unraveling Maintenance Mysteries: The Role of Root Cause Analysis in CMMS

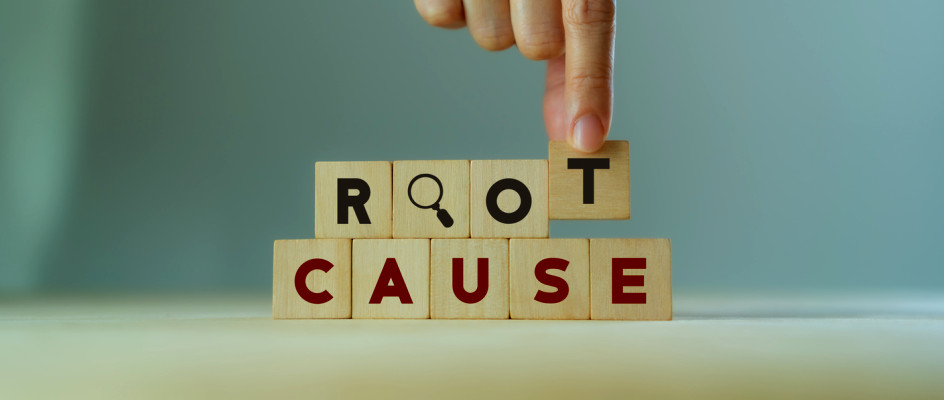
The quest for operational excellence involves not just fixing issues as they arise but understanding why they occurred in the first place. Root Cause Analysis (RCA) emerges as a crucial tool in this pursuit, unraveling the mysteries behind equipment failures and operational disruptions. In this comprehensive blog, we will explore what Root Cause Analysis is, its significance in the context of maintenance management, and how it forms the bedrock for learning from past maintenance experiences and predicting future breakdowns within the framework of a Computerized Maintenance Management System (CMMS).
Understanding Root Cause Analysis
Root Cause Analysis is a systematic process designed to identify the fundamental factors that contribute to a problem or failure. Rather than addressing only the visible symptoms, RCA digs deeper to uncover the underlying causes that, once resolved, can prevent the recurrence of issues. This methodology aims to move beyond the surface-level understanding of problems, fostering a more holistic perspective that enables organizations to make informed decisions and implement effective corrective actions.
The Fundamentals of Root Cause Analysis:
1. Identifying the Problem:
The first step in Root Cause Analysis is to clearly define the problem. This involves understanding the symptoms, disruptions, or failures that occurred, and their impact on operations. By precisely defining the problem, maintenance teams can focus their efforts on finding the root causes rather than merely addressing the symptoms.
2. Gathering Data:
Data is the lifeblood of Root Cause Analysis. Collecting relevant information about the problem, including historical data, maintenance records, and performance metrics, provides the foundation for a thorough analysis. In the context of CMMS, this data is often readily available, making it easier to trace the timeline of events leading up to the issue.
3. Investigating Causes:
With the problem defined and data in hand, the next step is to investigate the potential causes. This involves asking a series of "why" questions to trace the causal chain. RCA seeks to go beyond surface-level explanations and uncover deeper, often interconnected, causes that contributed to the problem.
4. Identifying Root Causes:
Root causes are the underlying factors that, when addressed, can prevent the recurrence of the problem. These causes are typically systemic rather than isolated incidents. Identifying the root causes requires critical thinking and a holistic understanding of the organization's processes, systems, and culture.
5. Implementing Corrective Actions:
Once the root causes are identified, the next crucial step is to implement corrective actions. These actions are designed to eliminate or mitigate the factors contributing to the problem. CMMS plays a pivotal role in this phase by facilitating the generation of work orders, tracking the progress of corrective actions, and ensuring accountability within the maintenance team.
6. Monitoring and Feedback:
Root Cause Analysis is an iterative process, and ongoing monitoring is essential to evaluate the effectiveness of corrective actions. CMMS provides a platform for continuous feedback, allowing organizations to track the performance of implemented solutions and make adjustments as needed.
Root Cause Analysis and CMMS
The integration of Root Cause Analysis within the framework of a Computerized Maintenance Management System (CMMS) elevates the entire maintenance management process. Here's why RCA is fundamental to the use of CMMS in learning from past maintenance experiences and predicting future breakdowns:
1. Learning from Past Maintenance:
CMMS serves as a comprehensive repository of maintenance data, encompassing work orders, equipment history, and maintenance logs. Root Cause Analysis, when integrated with CMMS, enables organizations to analyze past maintenance events systematically. By investigating the root causes of historical issues, maintenance teams can derive valuable insights into recurring patterns, failure modes, and areas for improvement.
2. Improving Decision-Making:
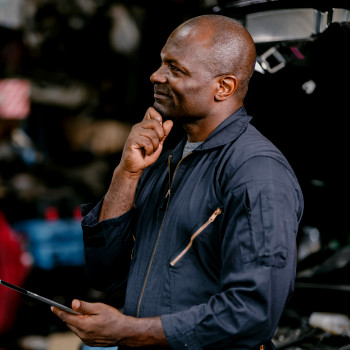
The insights gained from Root Cause Analysis contribute to more informed decision-making. CMMS provides a platform for visualizing data trends, identifying common failure points, and understanding the relationships between different variables. Armed with this knowledge, organizations can make strategic decisions to optimize maintenance strategies, allocate resources effectively, and prioritize preventive measures.
3. Enhancing Predictive Maintenance:
Predictive maintenance relies on the ability to anticipate and address potential issues before they lead to failures. Root Cause Analysis feeds directly into the predictive maintenance cycle by uncovering the fundamental reasons behind past breakdowns. By understanding these root causes, organizations can develop more accurate predictive models, allowing them to proactively address issues and prevent similar failures in the future.
4. Optimizing Preventive Measures:
Root Cause Analysis within CMMS enables organizations to fine-tune their preventive maintenance strategies. By identifying the root causes of past failures, maintenance teams can tailor preventive measures to address specific vulnerabilities and weak points in the system. This optimization enhances the effectiveness of preventive maintenance programs, reducing the likelihood of unplanned downtime.
5. Cultivating a Culture of Continuous Improvement:
Integrating Root Cause Analysis into CMMS fosters a culture of continuous improvement within the organization. By systematically analyzing the root causes of problems and implementing corrective actions, maintenance teams contribute to an environment where lessons learned from past experiences are applied to enhance future performance.
6. Documentation and Knowledge Sharing:
CMMS serves as a centralized hub for documenting Root Cause Analysis findings. This documentation becomes a valuable knowledge resource for the organization. Maintenance teams can refer to past analyses, share insights across departments, and ensure that the lessons learned from root cause investigations are disseminated throughout the organization.
Root Cause Analysis emerges as a guiding light, leading organizations from the shadows of reactive practices to the enlightened realm of proactive and predictive strategies. When seamlessly integrated into the robust framework of a Computerized Maintenance Management System, Root Cause Analysis becomes a catalyst for learning from the past, fortifying against future breakdowns, and cultivating a culture of continuous improvement. As organizations harness the combined power of RCA and CMMS, they embark on a journey towards operational resilience, efficiency, and a future where maintenance mysteries are not just solved but prevented altogether.