Define Your Maintenance Needs: A Strategic Approach to Selecting a CMMS

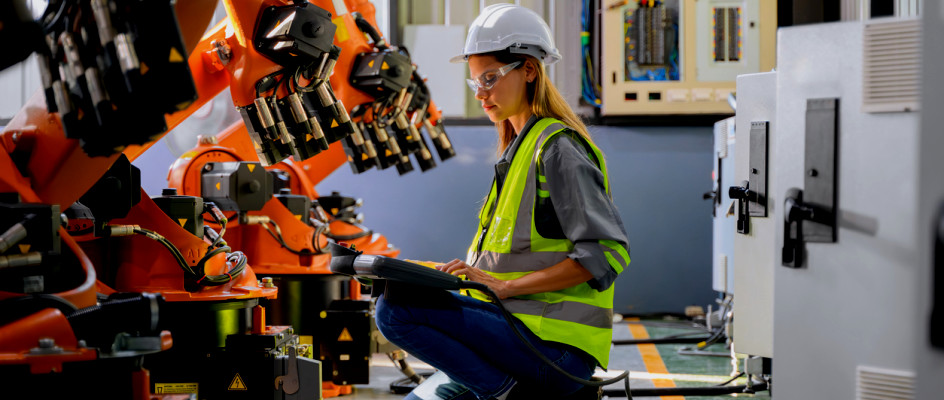
Before selecting a CMMS (Computerized Maintenance Management System), understanding your specific maintenance requirements is essential. This involves a thorough assessment of your assets, maintenance strategies, and operational goals. The more detailed your understanding, the better equipped you'll be to choose a CMMS that meets your needs and enhances your maintenance operations.
Nobody wants to go through the effort of researching, testing and then selecting a CMMS to find out some months later that it really wasn't the right product for their needs.
In a previous blog post, we discussed some steps to go through when selecting a suitable CMMS. Here, we'll expand on one element of that: Defining your maintenance needs.
Comprehensive Asset Assessment
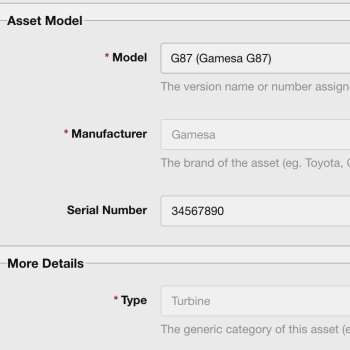
Begin by conducting a comprehensive inventory of all assets that require maintenance. This includes equipment, machinery, facilities, and even smaller tools or devices that play a critical role in your operations. Each asset should be documented with details such as:
Type of Asset: Identify whether it's a piece of machinery, a facility component, or another type of equipment. It is useful for future use because it helps tailor the maintenance strategy and optimize resource allocation. Understanding the asset type allows you to set appropriate maintenance schedules, track specific asset performance metrics, and plan for lifecycle management. This categorization also aids in forecasting future maintenance costs, ensuring regulatory compliance, and enhancing decision-making about upgrades, replacements, or retirements. Accurate asset identification ultimately improves overall operational efficiency and asset longevity.
Location: Record where the asset is situated, whether in a single location or across multiple sites. This helps streamline maintenance operations, optimize resource allocation, and ensure compliance with safety standards. Knowing the exact location of each asset allows for efficient scheduling of maintenance tasks, reducing downtime and travel time for technicians. It also aids in tracking environmental conditions that may affect asset performance, such as humidity, temperature, or exposure to corrosive elements. Accurate location data can also support strategic planning for asset upgrades, replacements, or relocations, enhancing overall asset management.
Manufacturer and Model: Note down the specifics, as these will be crucial for maintenance records and parts management. This is crucial for several reasons related to future use:
Maintenance Specifics: Different manufacturers and models have unique maintenance requirements, parts, and service schedules. Knowing these details ensures that the correct procedures are followed, reducing errors.
Parts and Inventory Management: It aids in sourcing the right spare parts and accessories, streamlining inventory management.
Warranty and Support: Accurate manufacturer and model information helps track warranties and avail technical support, ensuring that repairs and maintenance are cost-effective.
Performance Analytics: It allows for performance tracking and reliability analysis, helping identify trends and predict failures, which supports better asset lifecycle management and future procurement decisions.
Age and Condition: Understanding the age and current condition of the asset helps in planning maintenance schedules. This is important for future use because of:
Predictive Maintenance: Knowing the age and current condition helps predict when maintenance, repairs, or replacements will be needed, optimizing asset lifecycle management.
Budgeting and Planning: It aids in planning maintenance budgets by prioritizing older or poorly conditioned assets that may require more frequent attention or replacement.
Performance Evaluation: Tracking condition over time allows you to assess the performance and reliability of assets, guiding future purchasing decisions based on longevity and durability.
Safety and Compliance: Ensuring that aging assets are still safe and compliant with regulations helps prevent accidents and costly fines.
This inventory forms the foundation of your maintenance strategy, providing a clear picture of what needs to be maintained and at what intervals.
Maintainly has an import template that can be used to import large asset hierarchies. See Help to download it.
Categorize Assets Based on Criticality and Maintenance Frequency
Once the inventory is complete, categorize your assets based on their criticality and the frequency with which they require maintenance. Criticality refers to how essential an asset is to your operations. For example:
High-Criticality Assets: Equipment that is vital to production or safety should be prioritized. Downtime for these assets could lead to significant operational losses or safety hazards.
Medium-Criticality Assets: These are important but not mission-critical. Downtime might impact efficiency but won’t halt operations entirely.
Low-Criticality Assets: Non-essential assets that have minimal impact on overall operations.
Next, assess the maintenance frequency required for each category:
Preventive Maintenance: For high-criticality assets, preventive maintenance might be a priority to avoid unexpected failures.
Predictive Maintenance: Utilize condition-based monitoring for assets where downtime is costly, adjusting maintenance schedules based on real-time data.
Reactive Maintenance: Some low-criticality assets may only require maintenance when they fail.
This categorization allows you to tailor your CMMS selection to ensure it can handle the complexities of your specific maintenance needs.
Aligning CMMS Software Features with Maintenance Needs
With a clear understanding of your assets and their maintenance requirements, you can now align your CMMS selection with these needs. Consider the following features:
Asset Tracking and Management: Ensure the CMMS can handle detailed asset information, including the ability to manage multiple locations and asset types.
Maintenance Scheduling: Look for robust scheduling capabilities that allow for both preventive and predictive maintenance.
Work Order Management: The system should enable easy creation, tracking, and completion of work orders, prioritizing high-criticality tasks.
Reporting and Analytics: A good CMMS will offer comprehensive reporting tools that help analyze maintenance performance, costs, and asset longevity.
Integration with Other Systems: If you use other software tools, such as ERP systems or IoT devices, ensure the CMMS can integrate seamlessly.
By following this detailed, strategic approach, you'll be better positioned to choose a CMMS that not only meets your current maintenance needs but also adapts to future growth and changes in your operations. This thorough preparation ensures that your investment in a CMMS will yield significant returns in terms of efficiency, reliability, and cost savings.