Understanding the Maintenance Process: A Deep Dive into Efficiency and Reliability

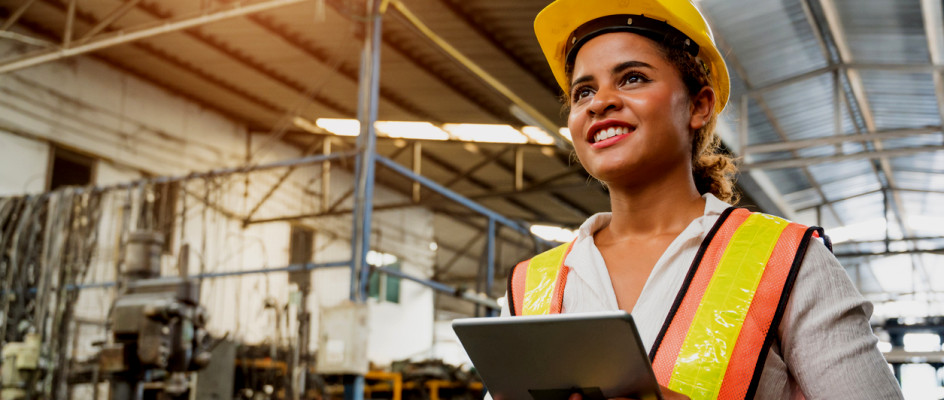
Maintenance Process for Efficiency and Reliability
Maintenance is a cornerstone of operational success in virtually every industry. From manufacturing and healthcare to transportation and hospitality, the ability to keep equipment and facilities running smoothly can significantly impact productivity, cost-effectiveness, and safety. At the heart of these benefits lies the maintenance process—a structured, strategic approach to preserving and enhancing asset performance over time.
In this blog post, we will explore the maintenance process in detail, breaking down its phases, types, benefits, and best practices. Whether you manage a facility, oversee a production floor, or operate a small business, understanding the maintenance process can empower you to minimize downtime, extend asset lifespan, and improve operational efficiency.
What Is the Maintenance Process?
The maintenance process refers to a systematic series of tasks designed to keep equipment, systems, and infrastructure in optimal working condition. It encompasses the planning, execution, and monitoring of maintenance activities to prevent breakdowns, fix issues, and ensure continuous operation.
An effective maintenance process involves a combination of preventive, corrective, predictive, and condition-based maintenance practices. These are applied based on asset criticality, usage, and environmental conditions.
Phases of the Maintenance Process
The maintenance process typically unfolds in the following phases:
1. Planning
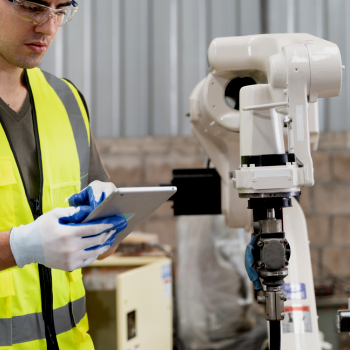
The first step is to plan the maintenance activities. This includes:
Identifying assets that require maintenance
Creating maintenance schedules based on manufacturer recommendations or usage data
Estimating time, labor, and resources needed
Preparing documentation and safety procedures
Proper planning helps avoid resource conflicts and ensures all tasks are executed efficiently.
2. Scheduling
Once tasks are planned, they are scheduled. Scheduling involves:
Assigning specific dates and times for each maintenance task
Allocating technicians or contractors
Ensuring equipment availability
Coordinating with production or operational schedules to minimize disruption
Advanced CMMS (Computerized Maintenance Management Systems) often automate scheduling and send reminders.
3. Execution
This is where the actual maintenance work is performed. Execution includes:
Performing inspections, servicing, repairs, or replacements
Following checklists and safety protocols
Documenting completed work
Technicians play a critical role in this phase. Their feedback can help refine future planning and identify recurring issues.
4. Documentation
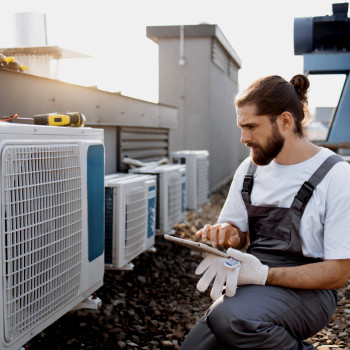
After tasks are completed, all actions must be documented. This includes:
Details of the maintenance performed
Parts used
Time taken
Observations or issues found
Accurate documentation supports compliance, cost tracking, and long-term asset management.
5. Review and Analysis
The final phase involves reviewing maintenance records and analyzing data to:
Identify trends or patterns
Optimize schedules
Make informed decisions about asset upgrades or replacements
Improve team performance
Using analytics tools built into CMMS software can provide powerful insights for continuous improvement.
Types of Maintenance in the Process
Understanding the different types of maintenance helps tailor your process for maximum efficiency:
Preventive Maintenance (PM)
This involves routine tasks done at regular intervals to prevent equipment failure. Examples include oil changes, filter replacements, and inspections. PM is proactive and reduces long-term costs.
Corrective Maintenance
Also known as reactive maintenance, this type occurs after equipment breaks down. It focuses on restoring functionality quickly but is generally more costly due to unexpected downtime.
Predictive Maintenance (PdM)
PdM uses data from sensors and monitoring devices to predict when maintenance should be performed. It helps avoid unnecessary tasks and target issues before they escalate.
Condition-Based Maintenance (CBM)
This strategy triggers maintenance when specific indicators show deterioration or performance decline. CBM is closely related to PdM but may not always rely on advanced analytics.
Benefits of a Well-Defined Maintenance Process
Implementing a structured maintenance process delivers a wide range of benefits:
1. Reduced Downtime
Unscheduled equipment failures can bring operations to a grinding halt, costing organizations in lost productivity, customer dissatisfaction, and expensive emergency repairs. Scheduled maintenance — the core of preventive and predictive strategies — helps eliminate these unexpected interruptions.
By identifying wear and tear before it leads to failure, businesses can plan maintenance during off-peak hours, minimizing operational disruption. Predictive tools like vibration analysis or thermal imaging go a step further, enabling maintenance teams to anticipate and address potential breakdowns with precision.
The result: fewer surprises, steadier workflows, and greater confidence in your production timeline.
2. Cost Savings
Preventive maintenance might seem like an upfront expense, but it saves organizations significant money in the long run. Emergency repairs often come with rush charges for labor and parts, not to mention the revenue lost from unexpected equipment downtime.
Moreover, when assets are well-maintained, they operate more efficiently and break down less often, reducing the need for costly replacements. Predictive maintenance tools also optimize resource usage by targeting only those components that truly need servicing — no more over-maintaining low-risk systems.
The result: a proactive maintenance strategy reduces both immediate repair costs and long-term capital expenditures.
3. Improved Safety
Safety is non-negotiable in any workplace — especially in industries like manufacturing, transportation, construction, and energy. Equipment that malfunctions due to poor maintenance can endanger workers, trigger accidents, and lead to serious injuries or even fatalities.
Regular maintenance ensures that all systems function within safe parameters and according to manufacturer specifications. For example, checking pressure valves, electrical systems, or conveyor belts can prevent dangerous malfunctions. Additionally, a solid maintenance record helps demonstrate due diligence in safety audits.
The result: when machines are safe, so are your people — and your organization stays on the right side of workplace safety regulations.
4. Enhanced Productivity
Well-maintained equipment performs better. Machines that are properly lubricated, calibrated, and aligned operate at optimal speed and quality, reducing waste and the number of defective products. Predictive and preventive maintenance also reduces the risk of slowdowns caused by minor malfunctions or bottlenecks.
Furthermore, maintenance processes help structure the workflow: teams know when machines will be offline for service and can plan around it. Less downtime means fewer delays and a more predictable production environment.
The result: more throughput, higher efficiency, and a more productive use of both labor and machinery.
5. Regulatory Compliance
Most industries are subject to strict regulations when it comes to equipment safety, environmental impact, and quality control. Failing to meet these standards can result in fines, shutdowns, or legal action — not to mention reputational damage.
Proactive maintenance helps organizations stay compliant by ensuring all equipment functions according to regulatory guidelines. Even better, a CMMS can automatically generate digital records of maintenance history, technician certifications, inspection dates, and other documentation needed during audits.
The result: maintenance isn’t just about performance — it’s also your frontline defense against non-compliance.
6. Asset Longevity
Equipment is one of the biggest capital investments a company makes. Maximizing its useful life is critical for return on investment (ROI) and asset value. When machines are neglected, their performance degrades, they consume more energy, and they fail sooner than expected.
Proactive maintenance — whether it’s replacing worn-out parts, cleaning filters, or recalibrating sensors — keeps assets running at peak condition. The longer they remain functional and efficient, the more value they generate over time.
The result: maintenance isn’t just about preventing failure; it’s about extending the performance window of your most valuable tools and systems.
Best Practices for Implementing the Maintenance Process
Expand each of the six items listed below.
To maximize the effectiveness of your maintenance process, consider these best practices:
1. Use a CMMS
Implementing a CMMS is one of the most impactful steps you can take to improve your maintenance workflow. A CMMS centralizes all your maintenance data — work orders, asset histories, parts inventories, technician schedules — into one accessible platform. This eliminates the chaos of spreadsheets, whiteboards, and disconnected documents.
With a CMMS, you can:
Automate preventive maintenance schedules
Track work orders in real time
Access maintenance histories instantly
Generate insightful reports for audits and KPIs
Moreover, cloud-based CMMS tools allow mobile access, so technicians in the field can update tasks, upload photos, and check off inspections from any device.
In short: a CMMS helps your team work smarter, stay organized, and make faster, data-informed decisions.
2. Prioritize Critical Assets
Not all equipment is created equal. Some machines are more integral to operations than others — either because they support core production, pose a higher safety risk, or are more costly to replace. That’s why asset prioritization is essential to effective maintenance planning.
By identifying your most critical assets and assigning them higher priority, you can:
Allocate resources more strategically
Reduce the risk of costly, high-impact failures
Extend the lifespan of your most valuable equipment
Tools like Failure Modes and Effects Analysis (FMEA) and risk-based scoring can help you assess criticality based on impact, likelihood of failure, and cost implications.
Bottom line: focus on what matters most first, and let your maintenance strategy scale outward from there.
3. Train Your Team
The best tools and plans mean little without a capable team to implement them. Investing in ongoing training for your technicians, planners, and managers ensures your maintenance staff is not only qualified but also aligned with the latest technologies and best practices.
Effective training should include:
Equipment-specific technical skills
CMMS software usage
Safety procedures and compliance training
Root cause analysis and problem-solving techniques
In addition to technical knowledge, soft skills like communication, time management, and collaboration should also be developed — especially as maintenance becomes more integrated across departments.
The takeaway: a knowledgeable and confident maintenance team reduces errors, improves safety, and boosts productivity.
4. Standardize Procedures
Consistency is key to high-quality maintenance. Standard operating procedures (SOPs) ensure that every task — from inspections to part replacements — is performed to the same standard every time, regardless of who is doing the work.
Benefits of SOPs include:
Fewer errors and omissions
Better training support for new team members
Easier compliance with safety and quality regulations
Improved scheduling and workload planning
SOPs should be written clearly, easily accessible (especially in your CMMS), and regularly updated to reflect changes in equipment or workflow.
In practice: SOPs act as the playbook for your team, reducing guesswork and increasing reliability across all maintenance tasks.
5. Monitor KPIs
If you can’t measure it, you can’t improve it. Key performance indicators (KPIs) provide the feedback loop needed to understand how well your maintenance program is performing and where adjustments are needed.
Some essential KPIs to monitor include:
Mean Time Between Failures (MTBF): Indicates equipment reliability
Mean Time to Repair (MTTR): Measures response efficiency
Planned Maintenance Percentage (PMP): Shows how much maintenance is proactive vs. reactive
Maintenance Backlog: Tracks outstanding work orders and potential risk areas
Regularly reviewing these metrics helps you identify bottlenecks, optimize preventive schedules, and justify budget allocations.
In short: KPIs turn your maintenance data into actionable insights that support continuous improvement.
6. Foster Communication
Maintenance doesn’t happen in a vacuum. It impacts — and is impacted by — departments like operations, safety, procurement, and finance. When communication breaks down between these groups, maintenance issues can escalate quickly.
Strong communication practices help:
Align maintenance schedules with production timelines
Coordinate shutdowns or repairs with minimal disruption
Speed up procurement of critical parts and materials
Improve reporting and regulatory compliance
Use tools like shared dashboards, real-time notifications, and digital work orders in your CMMS to keep everyone in the loop. And don’t underestimate the value of regular check-ins and cross-departmental meetings.
The result: a more collaborative, transparent maintenance culture that supports business-wide goals.
What Does Your Maintenance Process Look Like?
A structured maintenance process is essential for ensuring reliability, reducing costs, and maximizing the value of your assets. By understanding and implementing each phase—planning, scheduling, execution, documentation, and review—businesses can stay ahead of breakdowns, improve operational efficiency, and support sustainable growth.
Whether you are managing a single facility or multiple sites, adopting a robust maintenance process is a proactive step toward operational excellence. And with the help of modern CMMS tools, managing this process has never been easier or more effective. Now is the time to move from reactive to strategic maintenance—and reap the benefits for years to come.