What is CMMS?

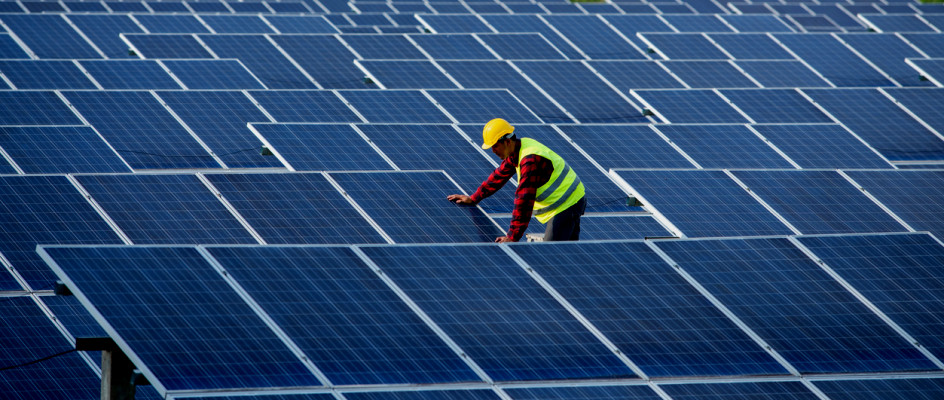
CMMS 101
CMMS stands for Computerized Maintenance Management System.
At the core of any CMMS is the asset hierarchy (often called the asset register). The asset hierarchy is essentially any valuable asset for which the asset history should be known and accessible, and on which work is to be performed and tracked.
Asset hierarchy serves as the backbone of a Computerized Maintenance Management System (CMMS) by providing a structured framework that organizes and categorizes assets within an organization. It establishes a clear and hierarchical relationship between equipment, systems, and components, reflecting the physical or logical connections among them. This hierarchical structure is fundamental for effective maintenance management, as it facilitates systematic organization, easy navigation, and streamlined data management. Asset hierarchy allows maintenance teams to quickly locate and assess specific assets, simplifies the assignment of work orders, and ensures accurate record-keeping of maintenance activities. By serving as the foundation for data organization and relationships, asset hierarchy enhances the efficiency, reliability, and overall functionality of the CMMS, enabling organizations to optimize their maintenance processes and make informed decisions about asset performance and lifecycle management.
The asset component is essentially what differentiates CMMS from more basic field service or work order software used by remote technicians that perform one-off jobs.
Work Orders
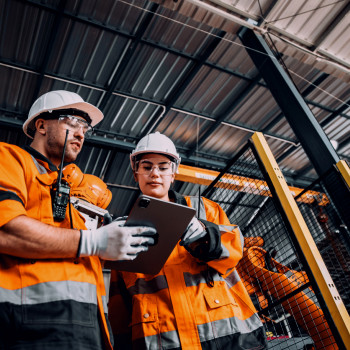
Work orders are essential tools within the realm of maintenance management, serving as a structured mechanism to initiate, track, and manage various maintenance tasks and activities. These documents play a crucial role in detailing the specifics of a maintenance request or job, providing a roadmap for maintenance teams to follow. Work orders typically include information such as the nature of the task, detailed instructions, the required resources, and any safety considerations. By centralizing this information in a standardized format, work orders streamline communication and coordination within maintenance teams, ensuring that everyone involved has a clear understanding of the tasks at hand. Furthermore, work orders contribute to efficient resource allocation, helping organizations prioritize and schedule maintenance activities based on their urgency and impact on operational continuity.
In addition to facilitating day-to-day maintenance operations, work orders are instrumental in establishing a comprehensive maintenance history for each asset. As work orders are completed, they become part of the asset's record, documenting the maintenance performed, parts replaced, and any issues addressed. This historical data becomes invaluable for preventive maintenance planning, trend analysis, and decision-making regarding asset lifespan. Ultimately, the use of work orders in maintenance management promotes organizational efficiency, transparency, and the long-term health of assets by providing a structured framework for planning, executing, and documenting maintenance activities.
Preventive maintenance
CMMS plays a crucial role in managing preventive maintenance (PM), also known as scheduled maintenance, by leveraging asset tracking functionalities. With assets being meticulously tracked within the CMMS, maintenance managers can efficiently plan and execute preventive maintenance tasks based on predefined intervals or criteria tailored to each asset. These intervals can be time-based, such as regular inspections or servicing conducted on a monthly, quarterly, or annual basis, ensuring that assets receive the necessary attention at appropriate intervals to maintain optimal performance and prevent unplanned downtime.
Additionally, CMMS enables meter-based preventive maintenance, where maintenance tasks are triggered based on meter readings or asset usage metrics. For example, a fleet of vehicles may undergo maintenance based on mileage readings, while production machinery may require servicing after a certain number of operating hours. By integrating meter readings into the CMMS, organizations can automate the scheduling of preventive maintenance tasks, ensuring that assets are serviced precisely when needed to prevent wear and tear, reduce the risk of failures, and extend asset lifespan. Furthermore, CMMS allows organizations to customize preventive maintenance schedules and criteria based on asset-specific requirements, industry best practices, and regulatory standards, providing flexibility and adaptability to evolving maintenance needs and ensuring compliance with maintenance protocols.
Reactive maintenance
Reactive maintenance, commonly known as "breakdown maintenance" or "run-to-failure," represents a maintenance strategy characterized by the performance of repairs and corrective actions on equipment or assets only after they have failed or experienced a malfunction. In this approach, maintenance activities are reactive in nature, initiated in response to unexpected breakdowns or disruptions in equipment performance. Unlike preventive maintenance strategies that prioritize proactive measures to address potential issues before they escalate, reactive maintenance relies on addressing problems as they arise, often resulting in unplanned downtime, costly repairs, and productivity losses.
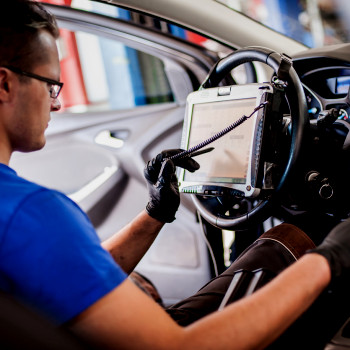
One of the key characteristics of reactive maintenance is its inherent unpredictability and lack of pre-scheduled maintenance plans. Maintenance tasks are triggered by equipment failures or malfunctions, leading to ad-hoc repairs and corrective actions aimed at restoring equipment functionality. This reactive approach can result in inefficiencies and resource wastage as maintenance personnel must mobilize quickly to address unexpected breakdowns, often requiring additional time and resources to diagnose and resolve the underlying issues. Moreover, reactive maintenance can lead to increased safety risks for personnel and equipment, as failure-related incidents may occur unexpectedly without warning, posing hazards to both workers and surrounding assets.
Despite its drawbacks, reactive maintenance may be employed in certain situations where the cost of implementing preventive maintenance measures outweighs the potential benefits. Organizations with limited resources or those managing non-critical assets with low failure consequences may opt for a reactive maintenance approach to minimize upfront costs and maximize asset utilization. However, reliance on reactive maintenance alone can result in higher long-term costs, decreased equipment reliability, and reduced operational efficiency. Therefore, organizations must carefully evaluate the trade-offs between proactive and reactive maintenance strategies to optimize asset performance, minimize downtime, and ensure cost-effectiveness in maintenance operations.
Inventory management
Most CMMS will also offer the ability to manage inventory. While CMMS does not strictly service inventory management, a natural extension exists given that spare parts and consumables are being consumed via work orders and they are an important factor in determining the cost of maintenance and of ownership of any asset over its lifetime.
Inventory components will usually include the ability to create a full spare parts list, stock locations or warehouses, as well as stock transfers and spare part purchasing to those locations. Barcoding systems will help identify parts, and well as assist with stocktaking and booking parts out.
Time tracking
CMMS will also capture work time. That is, the time technicians, or other user types for that matter, spend fixing issues or working on scheduled maintenance. Again, this is important data when considering the total cost of ownership of any asset.
More advanced CMMS or work order software will extend the capture of work time to include a timesheet facility and may even go further to the point of allowing you to integrate with payroll software and therefore create a seamless solution to avoid double entry of data for users.
Maintenance Analytics
A quality CMMS will provide ample reporting options to analyze several key metrics that are indicators of asset health, namely:
Downtime Tracking: CMMS records downtime incidents, helping organizations analyze the frequency and causes of equipment failures.
Equipment Reliability: Historical data on asset performance allows organizations to assess the reliability and availability of critical equipment.
Mean Time Between Failures (MTBF) and Mean Time to Repair (MTTR): CMMS calculates and presents key metrics like MTBF and MTTR, providing insights into asset reliability and maintenance efficiency.
Completion Rates: CMMS tracks the completion rates of work orders, enabling organizations to assess the efficiency of their maintenance teams.
Response Times: Analysis of response times helps identify areas for improvement in addressing critical maintenance issues promptly.